The Complete Guide to TPO Roofing
April 6th, 2023 | 13 min. read
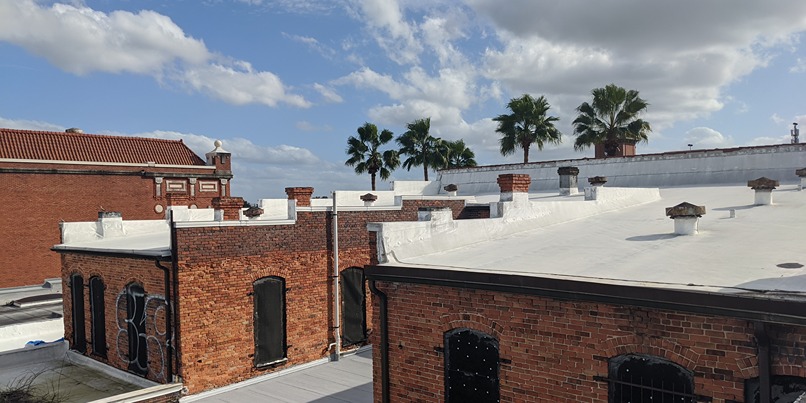
What is a TPO roof? TPO - which stands for Thermoplastic Polyolefin (TPO) - roofing is the most popular commercial roofing system on the market. But choosing a product based entirely on popularity can be disastrous. The roof system you need depends on your investment goals, your timeline, the type of building you're roofing, and your budget. The last thing you want is to spend hundreds of thousands of dollars on the wrong roof system.
So how good is TPO, and how do you know if it's right for your building?
These are the questions we answer in this guide.
At GIDEON, we've installed hundreds of thousands of square feet of every roofing system on the market, and we know the pros and cons of each. In the following guide, you'll learn what TPO is, what its strengths and weaknesses are, how it's installed, and whether it's the right choice for you.
Table of Contents
- What Is TPO Roofing
- Why TPO Is the Most Popular Roofing System
- Helps You Save on Labor Costs
- Holds Up Well in Most Weather
- Less Likely to Leak
- Helps You Save on Cooling Bills
- Disadvantages of TPO Roofing
- Not as Chemical or Oil Resistant as Other Roofs
- Less Fire-Resistant Than Other Single-Ply Systems
- Not Durable Enough for Industrial Environments
- May Be Damaged by Extreme UV Exposure
- How Is TPO Installed?
- How Much Does a TPO Roof Cost?
- When Is TPO Roofing a Good Roofing Choice?
- What Kind of Maintenance Does a TPO Roof Need?
What Is TPO Roofing?
Thermoplastic Polyolefin (TPO) roofing is a single-ply roofing membrane that originated in Europe and was introduced to the US in the 1990s. It's a tough, flexible thermoplastic polymer made of polypropylene, ethylene-propylene rubber, and additional filler components - a unique chemical makeup that allows it to handle a wide range of weather conditions. Not long after its introduction, it became the most popular roofing system in the US, accounting for around 40% of all commercial roofs.
It's called a "single-ply" roofing system because it consists of just one layer (the TPO membrane) instead of multiple layers or "plies." This distinguishes it from "built-up tar roofing" - the most popular roofing system for nearly a century - which consisted of multiple layers, or plies, of liquid asphalt and felt.
A complete TPO system consists of insulation, which is laid down on top of the roof deck or the previous roof system, and the TPO membrane, which consists of sheets that are 10, 12, or 20 feet wide. These sheets are rolled out over the insulation, cut to fit, and fastened either mechanically, adhesively, or with ballasts.
Why TPO Is the Most Popular Roofing System
TPO has several major advantages over other roof systems.
Helps You Save on Labor Costs
A huge reason TPO replaced the old built-up tar systems is that it is easier and safer to install. The old built-up systems used hot liquid asphalt, which was pumped up to the roof, and then rolled out over felt paper in three or four layers. It was hot, labor-intensive, and very smelly (not fun for the contractor or the people in the building, which sucked the smell in through the ventilation system). Contractors would also use a torch to seal the seams, which sometimes caused building fires.
TPO, by contrast, is very lightweight, can simply be rolled out and cut to fit, and the seams can be heat-sealed with a special heat gun rather than a flaming torch. When it is time to replace the roof, the membrane can be easily removed, and a new one rolled out and applied.
The material itself is also cheaper than other materials like EPDM and PVC. TPO membranes typically run around 65 cents per square foot, EPDM (ethylene propylene diene terpolymer - another single-ply roof system) runs around 90 cents per square foot, and PVC (also a common single-ply membrane) runs around $1.10 per square foot.
Holds Up Well in Most Weather
TPO is also very durable. The old tar roofs were more susceptible to ultraviolet radiation from the sun, which would cause them to leach plasticizers (chemicals that keep the asphalt flexible). The asphalt would then become brittle and crack.
TPO holds up well to UV radiation and can maintain its structural integrity and flexibility for around 20 years or more. TPO's thermoplastic membrane is also inherently resistant to water penetration, including ponding water (the phenomenon where water pools for long periods of time on a flat roof). And a properly-installed system is very wind-resistant (more on that when we discuss installation methods).
Less Likely to Leak
Roof seams are the areas where separate components of the roof come together. These can be penetrations (like a chimney or an HVAC unit) or where two different rolls of TPO meet. Seams are generally the first area of a roof to fail, so it is critical to seal them properly. TPO systems use heat-welded seams, which create a robust and watertight bond. Other roof systems, like EPDM roofs or modified bitumen, use adhesives, tapes, mechanical fasteners, or other cold-applied methods, which are less reliable than heat-welding.
Helps You Save on Cooling Bills
TPO is the most energy-efficient single-ply roofing system on the market. The white membrane is highly reflective, deflecting sunlight and reducing heat absorption. This energy-efficient feature minimizes the building's cooling expenses and complies with Energy Star and the Cool Roof Rating Council standards (CRRC).
Other systems, like EPDM and built-up roofs, are usually black, so they'll get very hot in the summer. PVC systems are white and highly reflective, but they tend to absorb a considerable amount of dirt, darkening the color and reducing reflectivity over time.
Disadvantages of TPO Roofing
Not as Chemical or Oil Resistant as Other Roofs
TPO roofing may not be suitable for industrial, restaurant, food-processing, or any other applications that are exposed to grease, oil, blood, or other chemicals. These substances can damage the TPO membrane and reduce its lifespan. PVC, in contrast, is highly durable and can withstand grease, blood, and many chemicals.
Less Fire-Resistant Than Other Single-Ply Systems
TPO is not as fire-resistant as other single-ply systems like PVC or acrylic roof coatings. In the early days, TPO was more fire resistant, but manufacturers discovered that the high amounts of fire retardant in the material made it brittle and prone to cracking. So they removed a significant amount of fire retardant, which solved the cracking issue but, of course, made TPO less fire resistant.
Not Durable Enough for Industrial Environments
Heavy foot traffic and mechanical equipment will cut and scratch the membrane and cause leaks.
May Be Damaged by Extreme UV Exposure
When the sun's UV rays are enhanced by reflection or are magnified in ponding water, the TPO membrane will deteriorate much more quickly than normal. This can occur when large windows or other reflective surfaces bounce the sun's rays back onto the membrane. Substantial ponding water ( ½ inch or more) can magnify the sun's rays as well. In both cases, the number or intensity of the UV rays is increased, shortening the effective life cycle of the membrane.
How Is TPO Installed?
There are three main steps in TPO installation:
Preparation
Preparing the substrate prior to installation is the crucial first step in TPO installation. Experienced contractors distinguish themselves in their attention to this step. A thorough inspection should be completed to make sure that any damaged roof decking is repaired or replaced, any drainage problems are discovered and addressed, and any existing roof materials or debris are removed. Leveling out the roof to address ponding water problems is a crucial step in preparation that a large number of contractors miss.
Insulation
The next step is to install proper installation onto the roof decking. The two most important factors to consider when choosing insulation are the R-value and the Perm rating. R-Value is the insulation's resistance to conductive heat flow. The higher the R-value, the more effective the insulation. Perm rating is a measure of the water vapor permeability. The higher the number, the more vapor can penetrate the insulation.
There are three common types of insulation:
Polyisocyanurate (polyiso) - A popular choice, Polyiso has the highest R-value of most insulation boards and a correspondingly higher price.
Expanded Polystyrene (EPS) - Commonly used in roof, wall, and floor insulation, EPS has the highest R-value per dollar.
Extruded Polystyrene (XPS) - XPS is priced and performs similarly to Polyiso and EPS. It has a perm rating of 1 and is semi-permeable.Polyisocyanurate (polyiso) - A popular choice, Polyiso has the highest R-value of most insulation boards and a correspondingly higher price.
Expanded Polystyrene (EPS) - Commonly used in roof, wall, and floor insulation, EPS has the highest R-value per dollar.
Extruded Polystyrene (XPS) - XPS is priced and performs similarly to Polyiso and EPS. It has a perm rating of 1 and is semi-permeable.Polyisocyanurate (polyiso) - A popular choice, Polyiso has the highest R-value of most insulation boards and a correspondingly higher price.
Expanded Polystyrene (EPS) - Commonly used in roof, wall, and floor insulation, EPS has the highest R-value per dollar.
Extruded Polystyrene (XPS) - XPS is priced and performs similarly to Polyiso and EPS. It has a perm rating of 1 and is semi-permeable.
Polyisocyanurate (Polyiso) - A popular choice, Polyiso has the highest R-value of most insulation boards and a correspondingly higher price.
Expanded Polystyrene (EPS) - Commonly used in roof, wall, and floor insulation, EPS has the highest R-value per dollar.
Extruded Polystyrene (XPS) - XPS is priced and performs similarly to Polyiso and EPS. It has a perm rating of 1 and is semi-permeable.
You can also add a cover board over the insulation and under the TPO membrane. This cover board provides a hard substrate that makes the membrane much more resistant to hail strikes and is necessary to achieve some FM Global Ratings (an insurance company that sets hail ratings).
Installing the Membrane
Once the insulation is in place, contractors will roll out the TPO membrane, making sure to avoid wrinkles and buckling while ensuring adequate roof coverage and overlap at the seams. The TPO membrane is then cut to fit the roof and make way for penetrations.
There are four methods of attaching a TPO membrane to a roof.
In a mechanically-attached system, fasteners and plates secure the membrane at regular intervals along the borders and seams. This is the least expensive and easiest to install, but also the least desirable. Mechanically attached systems allow the most airflow, making them the most prone to wind damage and the least energy efficient, and the fasteners create numerous penetrations that may be the source of leaks later on.
In a fully-adhered system, adhesive is applied to both the insulating boards and the bottom of the TPO membrane, and the membrane is pressed into place.
In a ballasted system, the membrane is rolled over the insulation, and heavy ballast materials are placed on top of it to keep the membrane in place.
In a wind-vented system, the membrane is loose-laid over the entire roof, like a ballasted system, but instead of securing it with pavers or rocks, an air seal with valves uses wind pressure to hold the membrane in place. This is an ingenious design because the harder the wind blows, the more tightly the membrane adheres to the decking. This makes it an extremely wind-resistant system.
How Much Does a TPO Roof Cost?
TPO is the least expensive single-ply system on the market. The cost of a TPO roofing system generally ranges between $6-$12 per square foot, including materials and labor. Multiple factors can influence TPO system pricing. For a more detailed discussion of roof pricing, check out our pricing guide.
TPO Material Costs
The price of TPO varies according to thickness, quality, and manufacturer. Thicker membranes are more expensive but last longer. Another major factor in the cost and quality of the TPO membrane is the type of "scrim" used. Scrim is a polyester-reinforced mesh fabric that is built into the membrane and gives it its strength and durability.
"Wicking" scrim is the least expensive and the least durable. It has a tendency to absorb water, which can damage the membrane over time.
Semi-wicking scrim is the next step up. It will absorb much less water.
Non-wicking scrim is the ideal (and the most expensive). It will not allow any water into the membrane.
The quality and thickness of the top coat are additional cost factors. The TPO polymer coat is where the TPO gets its typical white color, its fire rating, and its UV stability. Some manufacturers make it a point to add more thickness to their top coat to provide value and assure their sheet will perform as well or better than expected.
Other components, such as insulating boards, fasteners, adhesives, and flashing materials, will contribute to the project's final cost.
Roof Size & Complexity
Both the size and complexity of the roof significantly impact the final price of a project. Roofs with many penetrations, like vents, skylights, or HVAC equipment, are more labor-intensive, requiring cutouts and well-sealed seams. Roofs with steep slopes or irregular shapes may also need more effort and resources.
Ease of roof access is also important. If a roof requires additional equipment, like cranes or lifts, to access, your project will be more expensive. The area available for staging may also make a difference. A building located in a dense downtown with a limited area for staging will be more expensive than a building in an industrial park with plenty of parking lot space.
Location
Some municipalities may mandate that your roof meet certain criteria for fire resistance, wind resistance, or energy efficiency, which could require the use of certain installation methods, material types, or additional components. Permitting and inspection fees also vary by local jurisdiction.
Installation Method
Which installation method you select is another factor in your final price. Mechanically attached systems are the easiest to install and the least expensive but have the lowest performance. Fully-adhered systems have some of the best performance but are more expensive. Ballasted systems are generally inexpensive, but the ballast materials that hold them in place may damage the membrane and cause performance issues over time. Wind-vented systems are the most expensive but have the highest performance.
Warranty Length
As you would expect, systems with longer warranties are of higher quality and will cost more than systems with shorter warranties.
Tear-Off and Disposal
By law, you are allowed to have two roof systems installed on the same building, so you may be able to avoid this expense. But if you're already maxed out on roof systems, a tear-off will add substantially to your final cost.
When Is TPO Roofing a Good Roofing Choice?
There may be better choices for industrial environments than TPO. Why? Because, on its own, it is not durable enough to withstand harsh chemicals, heavy foot traffic or machinery, or impacts from sharp-edged tools and machines.
It may also not be a good choice for restaurants. As grease is removed from the air through the ventilation system, it often accumulates on the roof. Unlike PVC, TPO is not built to handle accumulations of grease.
Food processing plants are another contraindication for TPO, as it cannot withstand contact with waste byproducts, like blood. PVC, a highly durable membrane, is usually a better choice.
TPO may also not be the best choice if you are replacing an old but otherwise healthy roof. If, for instance, your roof warranty is about to expire, but your current roof has no major problems, you can extend the roof's life considerably with a less expensive roof coating system.
Outside of these situations, TPO is often the best choice for a new commercial roof.
What Kind of Maintenance Does a TPO Roof Need?
As with any asset, regular maintenance is key to keeping your roof in good condition and ensuring it lasts its intended lifespan.
We recommend pressure-washing the roof every few years.
Regular debris removal is also important, as it prevents water from pooling and reduces the risk of punctures or abrasions. Debris removal also ensures proper drainage.
If your membrane is torn or punctured, small repairs can be made using TPO repair tape or patches that are heat-welded in place. If the damage is extensive or complex, hiring a professional is recommended.
It's important to inspect your roof at least twice a year to catch any developing problems before they turn into major issues. A professional inspection by a competent professional is ideal. They will be able to spot any issues that an untrained eye will miss.
The Upshot
Finding the right commercial roof solution is time-consuming, and unless you are a roofing contractor, it's easy to overlook something important and make a bad purchase. Now that you've learned all about the pros and cons of TPO, we'd recommend getting on a free call with one of our GIDEON advisors. In 15-30 minutes, they can assess your current roofing needs and make customized recommendations for next steps.
Schedule a Free Call
Hop on a call with a GIDEON expert and learn more about how GIDEON can help you with your commercial roofing project.
Eric Schlossenberg started roofing when he was 24 years old, when he went to work as a Conklin contractor. Over the course of his career, he’s installed hundreds of thousands of square feet of roofing systems, but he still has a special passion for where he started in roof foam and coatings, and is a founding member of The Roof Coaters Guild of America. Gregarious and outgoing, Eric brings a unique sense of fun to his work, whether he’s on a roof or in the office.