The Problems with Commercial Roof Inspections…& How to Get a Good One
April 21st, 2023 | 8 min. read
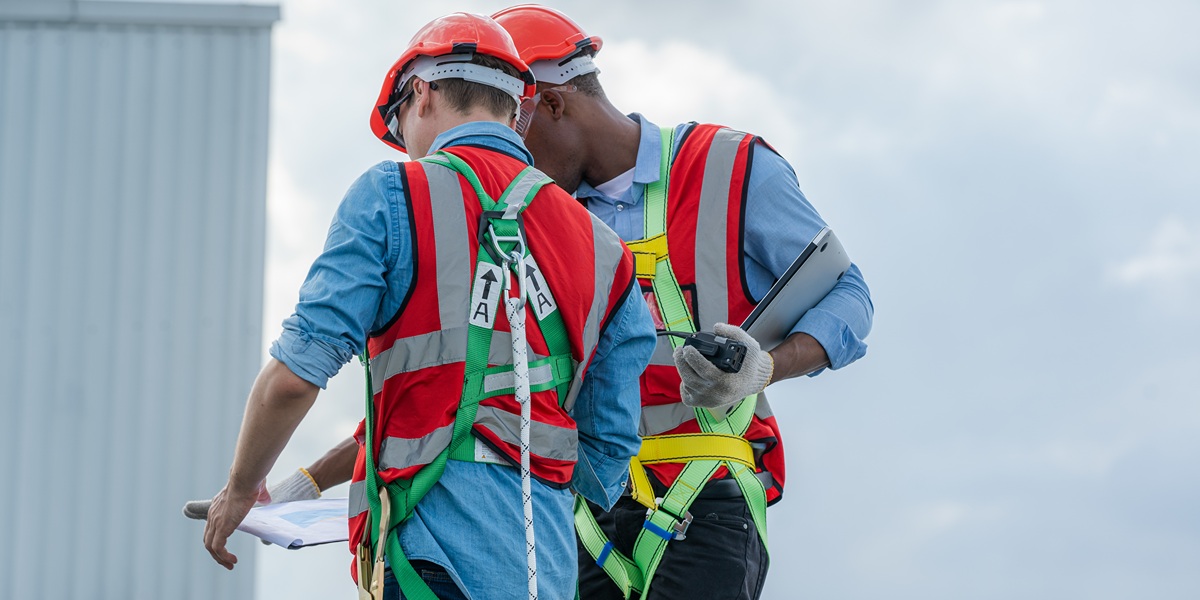
Would you like to pay for an expensive roof repair only to discover months later that you still have the same problem? We don't think so! Unfortunately, this is a widespread occurrence, and the number one reason is that the contractor didn't do a proper inspection.
At GIDEON, we've inspected thousands of roofs over the last twenty years, so we know what it takes to diagnose and fix your problem right the first time. In the following comprehensive guide, we'll discuss everything about roof inspections:
- What a good inspection looks like.
- What a bad inspection looks like.
- What you should know to ensure you get a good inspection from a reputable company.
The Dangers of a Bad Inspection
Comprehensive inspections are vital to diagnosing your roofing problem and providing an accurate quote. There are rarely easy, out-of-the-box solutions to roof damage. The contractor needs to understand what damage has been done, what kind of roofing system you have, what type of insulation you have, what kind of building you have, etc., to provide you with a real solution and a reliable quote.
What happens if you get a lousy inspection?
Wasted Time, Wasted Money, & a Leaky Roof
Unfortunately, not all roofing companies do a proper inspection. Many times, instead of sending a true expert to inspect your roof, companies will send salespeople. These salespeople often lack in-depth knowledge; their primary goal is to sell you a solution and make their commission. As a result, you may spend good money on a repair or a replacement, only to have the same problem in a year or two. Many facilities managers and building owners get into a cycle of hiring a contractor to fix a problem, discovering it didn't work, hiring a new contractor, finding their repair didn't work, etc. It's a vicious cycle we see too often.
What a Proper Roof Inspection Looks Like
Discovery Call
A good roof inspection begins, first and foremost, with a proper discovery call. The discovery call allows us to set up an inspection properly, which will save for both you and the roofer. A good roofing company will ask you three primary questions:
Where are you located?
This allows them to pull up your building on google earth. With this visual alone, they can get an idea of what kind of roof you have, how old it might be, and if there are any apparent problems.
How long have you owned the building, and what is its maintenance history?
This gives them an idea of the age of the system, where you are in the warranty period, and what kind of problems they might discover in the inspection.
Why are you calling a roofer now?
This is the most important factor in determining what type of inspection will be done. Customers generally fall into four categories:
1. You're selling the building
In this case, the contractor is likely to do a basic visual inspection for obvious signs of wear or damage, estimate the remaining roof lifespan, and ask you what the potential buyers plan on doing with the building. This last question is important because if the new owner intends to do something new with the building, it may be necessary to modify, coat, or even replace the roof. If they plan to put a restaurant in, for instance, the current roof membrane may not be able to handle grease from the ventilation system.
2. You just had a storm
In this case, a contractor should comprehensively inspect the top side of the roof, checking for hail, wind, or water damage. They should also help you file an insurance claim, and to that end, they should ask if you have photo documentation of the storm (to verify hail size, date, etc.) and storm duration.
3. You have a leak
In this case, the roofer will start with an interior inspection of the leak area to determine where it might be on the roof and what kind of decking you have, then proceed to a thorough inspection of the roof assembly, top to bottom. A core cut and infrared scan may be necessary to determine saturation.
4. You are coming to the end of your roof warranty
In this case, you need a comprehensive inspection of the roof assembly to determine if you can save the roof. In many cases, roofs at the end of their warranty have 40-70% life left and can be restored (with a brand new warranty) with a roof coating. This can save you a substantial amount of money, lowering your cost from around $8-$12 per square foot to $4-$6 per square foot.
Roof Assembly Inspection
Once they’ve learned what they need from the discovery call, a contractor will walk the roof and inspect the assembly. While the thoroughness of an inspection depends on several factors, as noted above, we'll use a comprehensive inspection as our example.
Penetrations, Seams, Flashings
Penetrations are anything that sticks through the roof membrane, such as HVAC units, chimneys, plumbing pipes, ventilation ducts, skylights, etc. Each of these creates seams in the roof that must be sealed, and sealant failure is the most common cause of leaks.
HVAC units can cause additional problems due to the water they collect from condensation. This water accumulates in a special pan inside the unit and frequently leaks onto the roof. Because the water is acidic, it can destroy the roof membrane over time.
They will also look at other seams, such as where two single-ply membrane panels come together, as well as flashing. Like seams in the membrane or around penetrations, these are the most likely to fail and cause leaks.
Drainage System
A good contractor will also inspect the drainage system, including gutter systems, gutter troughs, downspouts, and collector's heads. What condition are they in? How well do they remove water? Is anything clogged? Are they strong enough to hold weight, such as ice in the winter?
Walls
It's also essential to inspect the walls. What condition are the walls themselves in? Does the roof material properly adhere to the walls, or is it sliding off? What kind of coping do the walls have, and what is their condition?
Understanding the height of the roof wall is vital to an accurate scope of work. The National Roofing Contractors Association (NRCA) standard requires the walls to be 8 inches above the roof membrane. If they’re going to lay a new roof on top of an existing one, the roofing company may need to raise the walls. They may also need to raise the walls due to new regulations. Old buildings, for instance, require R-20 insulation, which is only 4-6 inches thick. Currently, regulations require R-30 insulation, which could be 6-16 inches thick. If you’re replacing R-20 with R-30, we may need to increase the height of your roof walls.
Roof Membrane
And, of course, the roof membrane needs to be inspected. Your contractor should check for ponding water, mechanical damage from repair technicians (or even falling bullets), and debris (volleyballs, trash, bottles, plant growth). They should also check for weathering (cracking, splitting, blistering) and any signs of improper installation, such as unnecessary overlaps or exposed fasteners.
For a single-ply membrane like TPO, we also perform a "tug test" to test how well the membrane adheres to the roof deck.
It is especially important to perform an analysis of ponding water, as its presence indicates that water has infiltrated the roof assembly, saturating the insulation and compressing the roof under its weight. The roofing company needs to understand the size and depth of the depression created by ponding water so it can not only fix the underlying water saturation but re-level the area to prevent ponding in the future.
It is also important to look for anomalies. An anomaly is where the membrane or roof system differs in appearance from one area to another. This could be caused by improper installation or a manufacturing defect. Correctly identifying this can allow you to file a claim on your roof's warranty and save you from paying for a repair or replacement.
Insect infestation is another important part of assessing the membrane that you don't want your contractor to miss.
Moisture Scan
A proper moisture scan may also be necessary. A contractor will look for trapped moisture inside the roof assembly using infrared imaging. Why is this necessary? Well, it's not unheard of for a contractor to discover that a large part of the roof is saturated with moisture and recommend a complete roof replacement. This may not be necessary, however, as the rest of the roof may be moisture free. With an infrared scan, you can determine exactly how much of the roof is saturated and potentially save thousands - if not tens of thousands - of dollars.
Core Samples
Taking a core sample means cutting into the roof to determine what the assembly is composed of. This allows us to determine what we will need to do during a repair or replacement. How many membrane layers are there? What kind of insulation was used in the original installation? What kind of mechanical fasteners does the roof use, 4-inch screws or 12-inch screws? This information is vital to creating an accurate scope of work and a proper price quote.
Unfortunately, not all contractors do a core cut, which can result in an inaccurate scope of work and costly change orders in the middle of a job. Imagine purchasing a $10,000 repair, only to learn halfway through that your contractor needs to add something to the scope of work, and it'll cost you another $8,000. It's not an uncommon situation.
Measurements
Last but not least, we need to obtain accurate measurements of the roof assembly to create an accurate scope of work and an estimate.
Comprehensive Report and Documentation
A good contractor gives you more than a verbal report and a few photos. A proper inspection report will include photos of all roof components inspected, particularly the problem areas, as well as detailed explanations of current conditions, the prognosis for your roof system, and what work needs to be done.
How to Prepare for a Roof Inspection
As a building owner or manager, proper preparation is essential to ensure a smooth and efficient commercial roof inspection. Here are some steps you can take to prepare for the inspection:
Plan the inspection: Schedule the inspection with the roofing firm at a suitable time. Choose a day with ideal weather conditions so that the inspector may safely access and evaluate the roof.
Notify tenants and employees: Inform your building's occupants and personnel of the scheduled inspection, as well as any anticipated interruptions or access needs. Provide them with the day and time of the inspection, as well as any sections that will be temporarily closed.
Clear the roof area: Remove any debris, equipment, or stored goods from the roof to allow us to access all areas.
Make interior spaces accessible: Make sure that the inspector has access to any internal locations that need to be examined, such as attics, higher floors, or ceilings.
Make yourself available for questions: During the inspection, make yourself or a qualified staff member accessible to answer any questions the inspector may have and offer extra information on the building or roof if needed.
Follow safety precautions: Let us know about any risks or areas of concern on your property.
Gather documentation: Provide us with any documentation you have on your roof, such as warranties, prior inspection reports, or records of previous repairs or installs.
The Upshot
The last thing you want to do is pay for something you don't need, or that doesn't work, or be surprised by an expensive addition to a job you already paid for. As we've discussed in this article, avoiding these costly SNAFUs starts with a proper inspection. Now that you've learned what a great inspection process looks like, go ahead and give GIDEON a call. In a free, 15-30 minute discovery call, we can help create a custom solution so you can get the job done right the first time.
Schedule a Free Call
Hop on a call with a GIDEON expert and learn more about how GIDEON can help you with your commercial roofing project.
Eric Schlossenberg started roofing when he was 24 years old, when he went to work as a Conklin contractor. Over the course of his career, he’s installed hundreds of thousands of square feet of roofing systems, but he still has a special passion for where he started in roof foam and coatings, and is a founding member of The Roof Coaters Guild of America. Gregarious and outgoing, Eric brings a unique sense of fun to his work, whether he’s on a roof or in the office.