TPO Roofing Cost: Everything You Need to Know
November 28th, 2023 | 8 min. read
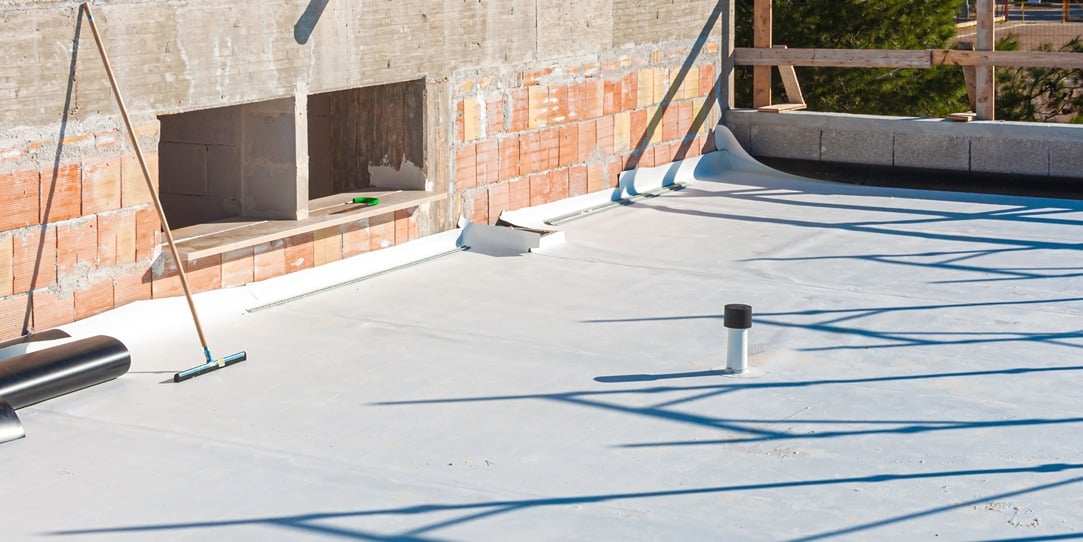
How much does a TPO roof cost?
If you’re in the market for a commercial roof replacement or repair, you may be looking at TPO roofing estimates from contractors and trying to decode exactly what you're paying for. With so many options and components involved, you can have trouble understanding not only what you’re paying for but what you should pay for.
At GIDEON, we're here to help. With over two decades of experience and a commitment to transparent pricing, we can make understanding the cost of your TPO roof a breeze.
In this article, we’ll break down the cost of a TPO roof into its core components, explaining how each factor affects the total cost.
Table of Contents
- TPO Membrane Cost
- How Installation Methods Affect TPO Roof Cost
- How Insulation Type Affects TPO Roof Cost
- How Labor Costs Affect The Price of a TPO Roof
- How Flashing Affects TPO Roof Costs
- Walk Track System
- Vinyl Protection Film
- Frequently Asked Questions
TPO Membrane Cost
When considering the overall cost of TPO roofing, one of the primary factors is the TPO membrane itself. This single ply roofing membrane is made from a blend of synthetic materials, primarily a thermoplastic polyolefin base that offers high flexibility and durability, making it the most popular commercial roof system in the US.
The price of a TPO membrane varies significantly, primarily influenced by the thickness of the membrane and the manufacturer. Typically, TPO roofing membranes come in a range of thicknesses, from 45 to 80 mils. A higher thickness often equates to better durability and a longer lifespan but also a higher cost. The standard mil thickness of a TPO membrane for a commercial roof is 60 mils.
On average, the membrane itself will cost around $.80 per square foot for the TPO membrane.
Remember that while the cost of the TPO membrane is an important factor, it's only one piece of the puzzle. You'll also need to consider installation methods, insulation types, labor costs, and more when calculating the total cost of a TPO roof.
How Installation Methods Affect TPO Roof Cost
The method of installation affects price substantially. There are four primary ways to install TPO roofing:
Mechanically Attached TPO Roof Systems
This is the most prevalent and typically the most economical method of installing TPO roofing. The membrane is attached to the deck using mechanical fasteners at designated intervals in this method. It's a relatively quick installation process that typically adds around $1.50 to $2.50 per square foot to the total cost. However, it might not be suitable for areas prone to high winds or roofs with complex designs.
Fully Adhered TPO Roof Systems
With this method, the TPO membrane is glued directly to the roof's surface, providing a flat, seamless appearance. It offers better wind uplift resistance and fewer seams than mechanically attached roofs. This installation process is more labor-intensive and, therefore, more expensive. It typically adds about $2.50 to $3.50 per square foot to the total cost.
Wind Ballasted TPO Roof Systems
In a wind ballasted system, the TPO membrane is loose-laid on the roof, and a wind venting system uses wind pressure to hold the roof in place. There are several advantages to the Wind Ballast method to attach a TPO Single-Ply membrane. By limiting or avoiding mechanical plates and fasteners, the roof system’s U-value (ability to insulate the building) is improved (avoiding thermal shorting) and installation times are cut down.
This installation method typically adds about $2.00 to $3.00 per square foot to the total cost.
RhinoBond TPO Roof Systems
Rhino-Bond is a newer option for attaching to the TPO membrane with minimal fasteners. This form of attachment relies on 3”insulated fasteners coated in TPO. The membrane is loose-laid over the assembly; magnets are used to locate the TPO-coated fastener plates, then a heat induction machine welds the TPO membrane directly to the top of the coated, insulated fastener plate. These systems are less expensive than a fully-adhered roof but have more wind uplift resistance than a mechanically attached roof. Typical cost ranges from $2-3 per sqft.
Your choice of installation method will depend on your building's specifics, local building codes, and weather considerations. A professional roofing contractor can provide invaluable advice on the best installation method for your needs and an accurate cost estimate.
How Insulation Type Affects TPO Roof Cost
Another critical component in the cost structure of a TPO roofing system is the type of insulation installed beneath the TPO membrane. The purpose of this insulation is to provide thermal resistance (R-value) and to provide a suitable surface for the membrane's application. The choice of insulation material can significantly affect the overall cost. Here are the most commonly used insulation types and how they impact the total cost:
Polyisocyanurate (Polyiso) Insulation
This is the most commonly used insulation in TPO roofing systems due to its high R-value and durability. It is also resistant to fire and moisture. It typically adds $0.70 to $3.50 sqft. A "tapered" Poly-ISO insulation system will easily run $2.50 to $3.50.
Expanded Polystyrene (EPS) Insulation
EPS (otherwise known as styrofoam) is more cost-effective than Polyiso, but - while it’ll keep your beer cold in the summer - it's a mediocre insulating material. It is lightweight and can be made into extremely thick pieces. This is helpful when the cost is an issue, and a tapered insulation system is required. It typically adds around $0.50 to $0.60 per square foot.
Extruded Polystyrene (XPS)
XPS sits between Polyiso and EPS in terms of cost and performance. It offers a good balance of price, R-value, and moisture resistance. This is the pink and purple insulation board found at Home Depot and Lowes that is often used in conjunction with siding. Although not a common flat roof insulation board, it outperforms EPS (styrofoam) by just a little bit. It typically adds around $0.60 to $0.70 per square foot.
The selection of the appropriate insulation material will depend on your building's specific requirements, the local climate, and energy efficiency goals. A professional roofing contractor can guide you in selecting the best insulation for your TPO roofing system.
How Labor Costs Affect The Price of a TPO Roof
On average, you can expect labor costs for TPO roofing to range between $0.50 to $2.00 per square foot, depending on the size, complexity, and amount of detail needed to flash walls and protrusions.
Labor costs can vary widely based on a variety of factors, including the complexity of the roof (for instance, the presence of roof penetrations like skylights or vents), geographical location, and the specific contractor you choose.
Keep in mind that choosing a contractor solely based on a lower cost could lead to problems down the line. It's important to ensure that your contractor has the right skills and experience to install TPO roofing. Installation errors can lead to a shorter lifespan for the roof and costly repairs, offsetting any initial savings. Always take the time to research and choose a reputable contractor, even if it means a slightly higher upfront cost. It's an investment that could save you significantly in the long run.
How Flashing Affects TPO Roof Costs
Flashing is an essential component of any roofing system, providing additional protection against leaks in areas of the roof where two surfaces meet, like around chimneys, HVAC curbs, walls, pipe penetrations, vents, and roof edges. Most TPO flashings are created in the field, though some flashing details have been prefabricated to form fit pipe penetrations, outside & inside corners, and Pitch Pans.
A general cost range for TPO flashing materials is around $5 to $10 per linear foot.
The total cost of TPO flashing depends on the number and type of roof penetrations and the complexity of the roof edge detail.
While flashing might seem like a minor detail, it is a critical part of ensuring the longevity and effectiveness of your TPO roof. Incorrectly installed flashing or opting for a lower-quality product to cut costs can lead to serious water damage over time. As such, it's crucial to budget adequately for high-quality flashing and professional installation.
Metal flashings such as face-mounted flashings, counter flashings, reglet flashings, and metal coping caps are common details on most TPO roof assemblies. These flashings are typically custom fabricated and specifically designed for each new roof. They allow water to "shed" from a vertical surface, typically adding additional protection to a TPO membrane terminated halfway up a wall. Metal coping cap covers the TPO membrane that has been wrapped up and over the top of the parapet wall.
Walk Track System
A final component, and one that can be overlooked by an inexperienced contractor, is a Walk-Trak system. A reputable contractor will design and install a path from roof access points to commonly maintained inventory on the roof, such as HVAC units and air handling units. Walk-Trak will be an add-on to any Scope of Work and typically runs $2.50-$3.50 per sqft of installed Walk-Trak.
Vinyl Protection Film
An often overlooked option that may be needed if you’re doing a TPO “reroof” is a vinyl protection film (Versico calls this APEEL). This protective vinyl film will protect the TPO membrane from dirt and soil contaminants and is typically used if you are roofing over or replacing a Tar & Gravel or black EPDM system. These roofs are extremely dirty - the asphalt dust and carbon from the EPDM membrane will get transferred to the new white TPO membrane by wind, foot traffic, and rooftop equipment. The vinyl protection film keeps the new TPO membrane clean and white and is simply peeled off after installation. This is an additional cost of $0.30 to $0.40.
The Upshot
From the price of the membrane to labor costs, insulation, installation methods, and additional components, understanding the cost of a TPO roof can be complex. But now that we’ve broken it down, you should have a very clear picture of what goes into the total cost.
As a next step, we invite you to reach out to our team. Whether you're ready to proceed with your TPO roofing project or have further questions, our professionals are ready to provide personalized advice tailored to your unique situation. Contact us today for a consultation, and let's ensure your next roofing project is a success.
Frequently Asked Questions
Q: How long does a TPO roof last?
A: A well-maintained, correctly-installed TPO roof will last 20 years or more. Unfortunately, many TPO roofs are installed incorrectly or maintained poorly and last only around 13 years.
Q: Can you walk on TPO roofing?
A: Yes, the TPO membrane by itself will handle light foot traffic. However, it’s best suited to install a Walk-Track system keeping employees and service vendors in designated areas to avoid footfall damage and potential costly repairs.
Q: What is cheaper, EPDM or TPO?
A: TPO is cheaper than an EPDM rubber roof membrane. The roofing industry has made TPO the commodity of commercial roofing. It was designed and manufactured to be an economical sheet that is based on the idea a commercial roof should be replaced approximately every 20 years.
Schedule a Free Call
Hop on a call with a GIDEON expert and learn more about how GIDEON can help you with your commercial roofing project.
Eric Schlossenberg started roofing when he was 24 years old, when he went to work as a Conklin contractor. Over the course of his career, he’s installed hundreds of thousands of square feet of roofing systems, but he still has a special passion for where he started in roof foam and coatings, and is a founding member of The Roof Coaters Guild of America. Gregarious and outgoing, Eric brings a unique sense of fun to his work, whether he’s on a roof or in the office.