Types of Corrugated Metal Roofing: 7/8 Inch vs 1/2 Inch
August 9th, 2023 | 8 min. read
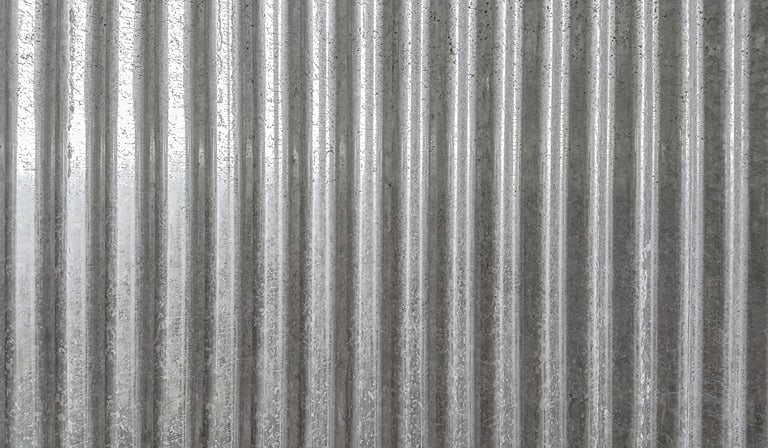
Corrugated metal roofs are one of the oldest and most popular types of roofs for agricultural, industrial, and warehouse buildings.
If you're interested in using corrugated metal for your next project, it's essential to understand the two types: the 1/2" corrugated and the 7/8" corrugated. It's also essential to understand what "corrugated" means in the roofing industry and what other types are available.
In this article, we're going to break it all down for you so you make an informed decision for your next roofing project.
Table of Contents
- What Is Corrugated Metal Roofing?
- Types of Corrugated Metal Roofs
- Advantages and Disadvantages of Corrugated Metal Roofs
- Installation of Corrugated Metal Roofs
- Other Technically Corrugated Metal Roofs
What Is Corrugated Metal Roofing?
Corrugated metal roofing is a type of roofing system with a distinctive rippled or 'wavy' appearance. The term 'corrugated' refers to the process of bending the metal sheets into a series of ridges and furrows, which substantially strengthens the metal, allowing for larger panels that are both lightweight and durable.
Typically made from galvanized steel, galvalume, or aluminum, corrugated metal roofs resist corrosion and can withstand very harsh weather conditions. Galvalume, which is steel coated in zinc, aluminum, and silicon, is especially popular due to its balance of affordability and longevity. Aluminum, on the other hand, is the most resistant to corrosion.
While other metal roofing types and styles can also be corrugated, the term 'corrugated,' when used in the roofing industry, specifies this unique "wavy S" structure, and excludes panels that have straight, angled shapes.
Types of Corrugated Metal Roofs
There are two primary and common types of corrugated metal roofing: 1/2" corrugated and 7/8" corrugated panels. The measurements, 1/2" and 7/8", refer to the height of the wave (or corrugation) in each panel.
Generally, the higher the height of the wave, the stronger the panel.
7/8" Corrugated Metal Panels
Advantages
The increased corrugation height boosts the panel's structural integrity and improves its ability to withstand harsh weather conditions, such as heavy snowfall or high winds. Their superior strength also allows them to span larger distances without an additional supports.
Disadvantages
Compared to 1/2" corrugated, 7/8" corrugated really has no disadvantages. 7/8" is stronger, considered better looking, is easier to install, and usually less expensive.
Prices
Prices for 7/8" corrugated metal panels can range from around $.90 to $1.50 per square foot, again depending on the material, finish, and gauge.
Ease of Installation
Because of 7/8" superior strength, it can be made into a much wider panel, reducing installation time and labor.
Colors & Finishes Available
7/8" corrugated panels come in virtually every color and finish, as 7/8" is easier to manufacture.
Best Applications
These panels are well-suited for almost any application, including residential buildings, industrial buildings, agricultural structures, and other larger structures in areas that are prone to heavy snowfall or high winds.
1/2" Corrugated Metal Panels
Advantages
Unfortunately, 1/2" corrugated roofing panels don't really have any advantages over 7/8" corrugated. The only reason to choose the former is if you prefer the aesthetics of the smaller corrugation.
Disadvantages
The smaller corrugations make the panels weaker, so they won't be able to span the same distances as 7/8", and they might not be as suitable for areas that experience heavy snowfall. 1/2" corrugated panels are also generally more expensive than 7/8".
Prices
1/2" corrugated panels will usually cost anywhere from $1.00 to $1.75 per square foot, depending on the specific material (steel, aluminum, etc.), finish, and metal gauge.
Ease of Installation
1/2" corrugated panels are smaller than 7/8", so more are needed, making installation more time-consuming and labor intense.
Best Applications
1/2" corrugated panels can be a solid choice for smaller commercial buildings and residences.
Colors & Finishes Available
While the colors available for any particular metal panel will from manufacturer to manufacturer, in the vast majority of cases, 1/2" corrugated will come in a much more limited set of colors than 7/8" corrugated. Why? Because manufacturing 1/2" corrugated panels is less economical for most fabricators than 7/8".
Advantages and Disadvantages of Corrugated Metal Roofs
Corrugated metal roofs come with a mix of benefits and downsides. Understanding these can help inform the decision-making process and help you choose the roofing type that best suits your needs.
Advantages of Corrugated Metal Roofs
Cost
Corrugated metal roofing is the least expensive of type of metal roofing.
Easy-To-Install
Despite their strength, corrugated metal panels are surprisingly lightweight, which eases the load on the building's structure and makes installation quicker and more manageable.
Fire Resistance
Metal is a non-combustible material, making corrugated metal roofs highly resistant to fire.
Design Variety
Corrugated metal roofs come in a wide array of colors and finishes, accommodating numerous architectural styles and personal preferences.
Disadvantages of Corrugated Metal Roofing
Not As Durable as Other Roofs
Because corrugated metal roofing panels only use exposed fasteners, they are prone to damage to due expansion and contraction.
As the metal roofing panel expands and contracts, screws can loosen and even pop out, and seams can become separated. All of this can create serious leaks.
The popular standing seam roof mitigates or avoids these issues by using a hidden, "floating clip" system that hides the fasteners and allows the panels to expand and contract without damaging the system.
Noise
During heavy rain or hailstorms, metal roofs can be louder than other roofing types. This issue can be mitigated by using more substantial roof decking, insulation, or sound-deadening underlayment.
Denting
While durable, corrugated metal roofs can be susceptible to denting from large hail or falling branches. However, some modern metal roofing materials are designed to be impact-resistant.
Installation of Corrugated Metal Roofs
When it comes to the proper installation of corrugated metal roofs, a series of critical steps, precautions, and expertise are involved. The following outlines this process in detail.
Preparation: First and foremost, every installation begins with a thorough assessment of the existing roof, ensuring that it's structurally sound to support a new corrugated metal roof. This step often involves cleaning the roof and removing any debris or old roofing materials.
Safety Measures: Installation of corrugated metal roofs requires proper safety measures. These include wearing the appropriate personal protective equipment (PPE), like gloves, safety glasses, and non-slip footwear. It's also crucial to use secure ladders or scaffolding for safe roof access.
Underlayment Installation: Underlayment serves as a secondary barrier against water and wind-driven rain. It is installed over the roof deck before the metal panels. This material also aids in energy efficiency by preventing panel noise and provides an additional layer of insulation.
Layout Planning: This stage involves the accurate measuring and cutting of roofing panels. It's essential to allow for an overhang of the panels at the eaves to control water runoff. The panels should be laid from the bottom up, starting from the furthest corner away from the prevailing wind direction.
Panel Installation: Installation starts at the lowest point of the roof, typically at the eaves, moving upwards toward the ridge. Panels overlap along the edges, generally by one corrugation, to ensure a watertight seal. They are secured using screws with neoprene washers, which help seal the holes and prevent leaks.
Flashing Installation: Flashing is used at the joints, intersections, and edges of the roof to prevent water ingress. It is installed around features like chimneys, vents, and at the roof peaks and valleys. Proper flashing is crucial in maintaining the roof's integrity and preventing leaks.
Sealing: Once the panels and flashing are installed, all seams, joints, and fasteners are sealed with a high-quality sealant to provide an additional barrier against potential leaks.
Inspection: After the installation is completed, a final inspection is necessary to ensure that all components have been properly installed and sealed. This step includes checking the alignment of panels, the tightness of fasteners, and the adequate sealing of joints and seams.
Installation of corrugated metal roofs is a complex process that requires meticulous attention to detail and skilled workmanship. Due to the intricacies and the risks involved, it is often advised to employ professionals for the task. DIY installation is an option, but it should only be undertaken with a solid understanding of the process and proper safety precautions.
Other Technically Corrugated Metal Roofs
While corrugated metal roofing typically brings to mind the classic wavy S-pattern, the roofing industry includes other types of metal roofing types that, although technically corrugated, significantly differ from traditional corrugated metal roofs in profile, installation, and application. The focus here is on three such types: R-panels, PBR panels, and standing seam roofs.
R-Panel Metal Roofs
R-Panel roofs, an alternative to the typical corrugated style, feature linear, high ribs set at larger intervals. Though they are corrugated, their straight-edge design gives them a different aesthetic. They are commonly found on warehouses and industrial buildings.
PBR-Panel Metal Roofs
PBR panels are a variant of R-panels, earning their designation from the "purlin-bearing leg," a feature that increases overlap between panels for enhanced waterproofing. They tend to be more costly than standard R-panels, but their superior water resistance can be a significant advantage.
Remember, when we discuss 'corrugated' in the roofing industry, it is generally in reference to the traditional wavy-patterned metal roofs. While R-panels, PBR panels, and standing seam roofs may fall under the corrugated category due to their ridged surfaces, they are distinctly different and merit separate and thorough discussions.
The Upshot
Choosing the right metal roof is not always easy, but fortunately, the choice between 1/2" and 7/8" corrugated is (7/8" is the clear winner), now that you've learn all about the differences between these two types of panels, plus a little extra on corrugated roofing in general, reach out to us. In a free, 30 minute consultation, our nationally-recognized roofing experts can provide you with customized guidance on your roofing project.
Schedule a Free Call
Hop on a call with a GIDEON expert and learn more about how GIDEON can help you with your commercial roofing project.
Eric Schlossenberg started roofing when he was 24 years old, when he went to work as a Conklin contractor. Over the course of his career, he’s installed hundreds of thousands of square feet of roofing systems, but he still has a special passion for where he started in roof foam and coatings, and is a founding member of The Roof Coaters Guild of America. Gregarious and outgoing, Eric brings a unique sense of fun to his work, whether he’s on a roof or in the office.