Spray Foam Roofing: A Complete Guide
August 18th, 2023 | 15 min. read
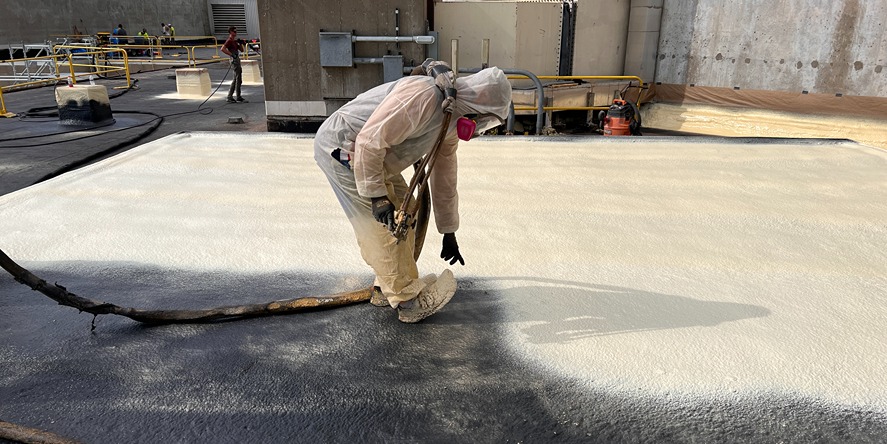
Spray foam roofing has revolutionized the way we protect and insulate our buildings, providing a seamless, energy-efficient solution that's as innovative as it is effective. But what exactly makes spray foam roofing so unique, and how can it transform a commercial building?
In this complete guide, you'll learn all about this cutting-edge roofing method, from its exceptional durability to its unparalleled insulation properties.
Whether you're a building owner or a seasoned contractor this guide is tailored to demystify spray foam roofing and illustrate why it might be the perfect fit for your next project.
Table of Contents
- What is Spray Foam Roofing?
- The Benefits of Spray Foam Roofing
- Spray Foam Roofing and Corporate Sustainability
- Cons of Spray Foam Roofing
- Costs of Spray Foam Roofing
- Installation Process of Spray Foam Roofing
- Comparison of Spray Polyurethane Foam (SPF) to Other Roofing Systems
What is Spray Foam Roofing?
Spray polyurethane foam is an insulating material that has been used extensively in a variety of building applications for over 60 years. Its unique physical properties – namely, its ability to be sprayed as a liquid and harden into a seamless, monolithic barrier of insulation – make it highly versatile and effective.
In the roofing world, spray foam is combined with an elastomeric coating to create an extremely powerful roofing system that can be applied over an existing roof, preventing the need for tear off and dramatically improving the energy efficiency and strength of the original roofing system.
A spray foam roof system consists of three primary components: the substrate, the polyurethane foam, and the elastomeric coating.
The process begins with a thorough cleaning and repair of the substrate (which can be a roof deck or an existing single ply or other kind of roof membrane).
This is followed by the application of SPF, which expands up to 30 times its original volume upon application, forming a hard, seamless, monolithic foam surface.
The foam is then coated with the elastomeric top coat, which can be made of acrylic, silicone, or urethane. This top coat provides a durable, waterproof, and UV-resistant barrier, protecting the underlying foam.
The final product is a seamless, monolithic roofing system that is lightweight, durable, flexible, and extremely energy efficient.
The Benefits of Spray Foam Roofing
1. Energy Efficiency
One of the most notable benefits of spray foam roofs is their exceptional energy efficiency. This efficiency is due, in large part, to SPF's high R-value and low U-value. In the language of insulation, R-value is a measure of thermal resistance, i.e., how well a material prevents heat from flowing through it.
The higher the R-value, the better the insulating performance. SPF roofing has one of the highest R-values per inch of all insulating materials.
U-value measures the amount of heat that can be transferred through an entire roofing system as a whole. The U-value takes into account gaps and seams between insulating panels as well as the presence of metal fasteners.
In traditional insulation (like the XPS boards in the picture below) gaps and seams create "thermal bridging", wherein airflow transfers thermal energy; metal fasteners conduct thermal energy in a process called "thermal shorting.
The lower the U-value, the better the material is at insulating. Spray foam roofing has an exceptionally low U-value because it is seamless and does not require metal fasteners.
Energy-efficient buildings are not only more comfortable for occupants, but they also significantly cut down on heating and cooling costs. This is particularly beneficial for large commercial facilities where energy costs can be a significant operational expense.
2. Waterproofing Capabilities
Another significant benefit of SPF roofing systems is their excellent waterproofing capabilities. When spray polyurethane foam is applied, it forms a seamless, monolithic layer across the entire roof. This foam layer fills in cracks, seams, and penetrations in the existing roof substrate, effectively eliminating potential pathways for water intrusion.
Moreover, the foam's closed-cell structure makes it inherently waterproof. Even if the roof's surface is somehow damaged, water cannot seep into the foam and spread throughout the roof system. This is a distinct advantage over other roofing systems, where a breach in the surface can lead to widespread water damage within the roof system.
3. Easy Maintenance
SPF roofing systems are also relatively easy to maintain. The primary maintenance requirement is the periodic inspection and recoating of the elastomeric top coat. This top coat is crucial for protecting the underlying foam from the sun's harmful UV rays, maintaining the roof's reflectivity, and ensuring its continued waterproofing and insulating performance.
Over time, the elastomeric coating can wear away, particularly in high-traffic areas. When this happens, the affected area can simply be cleaned, recoated with more elastomer, and the roof is good as new. This recoating process can be repeated indefinitely, making SPF a renewable roofing option.
4. Lightness
When considering roofing materials, weight is often a crucial factor, particularly for large commercial buildings. Here again, spray foam roofs have a distinct advantage. Despite its durability and performance, SPF is exceptionally lightweight, weighing only about 8 ounces per square foot. This is significantly lighter than other roofing materials.
5. Durability
Finally, SPF roofing systems offer remarkable durability. Although spray foam is relatively soft compared to materials like metal or concrete, it has a unique ability to flex with the building's movement, reducing the likelihood of cracking or breaking under normal conditions.
Its resilience to foot traffic and hail damage is a result of the elastomeric top coat, which is both durable and flexible.
In summary, the benefits of SPF roofing systems are manifold. Their exceptional energy efficiency, waterproofing capabilities, easy maintenance, lightness, and durability make them an attractive option for a wide range of applications.
Spray Foam Roofing and Corporate Sustainability
As businesses worldwide grapple with the ever-pressing need for more sustainable practices, the potential for spray foam roofing to contribute to these efforts should not be overlooked.
In the current era, where Environmental, Social, and Governance (ESG) considerations significantly shape corporate behavior, the adoption of SPF roofing systems can play a significant role in attaining a company's sustainability targets, contributing to corporate sustainability in several ways.
1. Energy Efficiency and Reduced Carbon Footprint
Most commercial buildings are major energy consumers, particularly for heating and cooling. High energy consumption translates into high levels of greenhouse gas emissions, due to reliance on fossil fuels.
With a high R-value and a low U-value, spray foam roofs can substantially reduce down energy consumption, not only helping you save on energy costs, but also lowering your carbon footprint.
2. Resource Efficiency and Waste Reduction
Another core element of sustainability is resource efficiency, particularly in the use and management of materials. Spray foam roofing promotes resource efficiency in several ways.
Firstly, SPF roofing systems are often installed directly over an existing roof system, without the need for a costly and waste-generating roof tear-off. This avoids disposing of old roofing materials in landfills and saves the energy and resources needed to manufacture and transport new roofing materials.
Secondly, the durability and renewability of SPF roofs contribute to resource efficiency. With the right maintenance, a spray foam roof can last indefinitely, eliminating the need for replacement and the associated waste and resource consumption.
Finally, the superior performance of SPF means that less material is needed to achieve the same insulating effect - another win for resource efficiency.
3. Improved Indoor Environmental Quality
The social component of ESG is equally important and often relates to the welfare and well-being of employees and other stakeholders. Spray foam roofing systems can contribute to improved indoor environmental quality by creating a more stable and comfortable indoor climate.
This can lead to improved productivity and reduced health issues associated with poor indoor air quality.
4. Long-term Economic Sustainability
While the environmental and social aspects of sustainability often get the most attention, the economic aspect cannot be forgotten. For a business to be truly sustainable, it must be economically viable in the long term.
The cost-effectiveness of SPF roofing systems contributes to economic sustainability by reducing both immediate and long-term costs. The immediate cost savings come from the ability to overlay the spray foam onto existing roofs, avoiding the expense of roof tear-off and disposal.
Long-term cost savings come from several sources. Reduced energy costs due to improved insulation can save significant amounts of money over the roof's life. The durability and renewability of the SPF system mean that replacement costs can be avoided. And the ease of repair keeps ongoing maintenance costs low.
Cons of Spray Foam Roofing
While the benefits of spray foam roofing are significant, SPF roofing is not without its cons.
Here are some notable potential disadvantages to consider.
1. Overspray
One of the challenges faced during the installation of spray foam roofing is the risk of overspray. Overspray occurs when, during application, some of the SPF particles are carried away by the wind and land on surfaces where they are not intended to be. These surfaces could include nearby cars, buildings, or landscape features. Overspray can be a considerable concern, especially in populated areas with lots of adjacent properties and structures.
It's important to note, however, that overspray can be managed effectively. A skilled spray foam roofing contractor will be aware of the risk and take precautions such as using screens to protect nearby areas and carefully monitoring the weather to choose optimal conditions for the spray application.
2. Weather Limitations
The installation of spray foam roofs is subject to weather conditions. The process requires dry and relatively warm conditions for the foam to cure properly. Humidity can affect the foam's ability to adhere to the roof, while cold temperatures can interfere with the chemical reaction that causes the foam to expand and cure. These weather constraints can lead to scheduling issues for installation.
3. Finding Qualified Installers
As with any specialized trade, finding qualified, experienced SPF installers can be a challenge. The installation of spray foam roofing requires a high level of skill and experience to avoid problems like improper mixing, incorrect thickness, and poor adhesion to the substrate. Mistakes during the installation process can result in a less effective roof system that may fail prematurely or not deliver the expected benefits.
Therefore, it is crucial to work with a spray foam roofing contractor who has a solid track record, the necessary certifications, and positive customer reviews. The Spray Polyurethane Foam Alliance (SPFA) is a professional organization that offers training and certification for spray foam installers, and choosing a contractor with SPFA certification can help ensure a quality installation.
Despite these potential drawbacks, spray foam roofing remains a robust choice for many commercial buildings due to its superior insulation properties, durability, and contribution to sustainability goals. However, it is essential to consider these potential downsides and work with a competent roofing contractor to mitigate risks and ensure a successful SPF roof installation.
Costs of Spray Foam Roofing
When considering a new roofing system, one of the key factors that come into play is the cost. The investment in a new roof can be substantial, so it is critical to understand the various cost factors associated with different roofing systems. When it comes to spray foam roofing, there are several aspects to consider, including installation, maintenance, and potential savings in energy costs.
1. Installation Costs
The cost of installing a spray foam roof will depend on several factors. These include the size and complexity of the roof, the thickness of the foam layer, the type of protective coating used, and the labor costs in the area. As a general rule, the cost of spray foam roofing ranges from $2.5 to $6 per square foot for a fully installed system, including both the spray foam layer and the protective coating. This cost might seem high compared to other roofing systems, but it is important to consider the long-term benefits and potential savings associated with SPF roofing.
2. Maintenance Costs
One of the benefits of a spray foam roof is its low maintenance costs. Generally, an SPF roof requires minimal maintenance compared to other roofing systems. We recommend an inspection once every 6 months to check for any damage and ensure the protective coating is still in good shape. Usually the coating needs to be reapplied once very 10-20 years (depending on the type of system), and this will typically cost between $2 and $5 per square foot. This recoating can extend the life of the roof by another 10 to 20 years, and gets you a brand new warranty, making it extremely cost-effective in the long-run.
3. Energy Cost Savings
When evaluating the cost of a spray foam roof, it's critical not to overlook the potential savings on energy costs. On average, the energy savings from an SPF roof can cover the cost of the installation within 5 to 7 years. After this period, the continued energy savings are essentially money in the pocket.
4. Comparison to Other Roofing Systems
When comparing the cost of spray foam roofing to other systems, it's important to take a long-term perspective. While the initial investment for an SPF roof might be higher than some other types of roofs, the total life-cycle cost, including maintenance and energy savings, often makes it a more economical choice over the long term.
Installation Process of Spray Foam Roofing
The installation process of spray foam roofing (SPF) is a complex but efficient task that must be carried out by professional contractors to ensure optimal performance. Here's a detailed step-by-step guide on how this process unfolds:
1. Preparation of the Existing Roof
The first step in the installation process involves preparing the existing roof substrate for the application of the spray foam. This step involves thoroughly cleaning the roof surface to remove any debris, dust, or loose particles. If the existing roof has any damage or deteriorated areas, they must be repaired or replaced. In some cases, an old or incompatible roof system may need to be entirely removed, in a process called a roof tear-off. The preparation stage also includes ensuring that the roof is dry, as moisture can affect the adhesion and efficiency of the spray foam.
2. Spraying the Polyurethane Foam
Once the roof is prepared, the next step is to apply the spray polyurethane foam. This process is carried out using a specialized machine that mixes two liquid components together - the polyol/resin and the isocyanate. When these two components are combined under high pressure in the spray gun, they react to create the polyurethane foam. The resulting foam is sprayed onto the roof, where it expands and hardens, creating a solid layer of insulation that conforms to the roof surface.
The thickness of the foam layer will depend on the specific requirements of the building, such as the desired R-value (thermal resistance) and structural load considerations.
3. Applying the Protective Coating
After the spray foam has cured, a protective coating is applied. This coating is crucial as it protects the foam from the sun's UV rays, which can break down the foam over time. It also provides a waterproof layer, enhances the foam's fire resistance, and can improve the roof's aesthetic appearance.
The most commonly used coating is an elastomeric coating, such as acrylic, silicone, or polyurethane. The choice of coating will depend on the specific conditions and requirements of the roof, including the climate and the roof's exposure to foot traffic or other potential sources of damage.
4. Regular Inspections and Maintenance
Once the spray foam roofing system is installed, it is important to have regular inspections and perform necessary maintenance to ensure the longevity and performance of the roof. Generally, an SPF roof should be inspected at least once every year, and after any severe weather events.
It's also important to note that weather conditions play a crucial role in the installation process of an SPF roofing system. The foam should be applied when the temperature is above 50 degrees Fahrenheit and there is no risk of precipitation. The coating should be applied when the temperature is above 55 degrees Fahrenheit. Therefore, the installation process needs to be properly planned with weather forecasts in mind to ensure optimal application conditions.
In conclusion, the installation process of a spray foam roof is a detailed process that requires professional knowledge and equipment. But when properly installed, an SPF roofing system can offer significant benefits in terms of energy efficiency, durability, and longevity.
Comparison of Spray Polyurethane Foam (SPF) to Other Roofing Systems
1. Single Ply Roofing
Single ply roofing is composed of flexible sheets of compounded plastic-derived material. The most common types are TPO (thermoplastic olefin), PVC (polyvinyl chloride), and EPDM (ethylene propylene diene monomer). These sheets are rolled onto the roof surface and then adhered with adhesive, mechanically fastened, or heat-welded at the seams.
While the cost of single ply roofing can vary depending on the material type and installation complexity, it's typically less expensive than SPF upfront but does not offer the same level of insulation - and thus energy savings and environmental benefits. It also will need to be replaced. Installation can be more labor-intensive, especially for larger commercial roofs, and less adaptable to irregular roof shapes compared to SPF.
2. Built-Up Roofing (BUR)
Built-up roofing, often referred to as "tar and gravel" roofing, is one of the oldest and most traditional types of roofing. It's built up with alternating layers of bitumen (asphalt or coal tar) and reinforcing fabric, topped with a layer of gravel or crushed stone to protect against UV radiation and weathering.
The cost of BUR systems is generally lower per square foot than SPF, but BUR can be more expensive when you factor in maintenance and replacement costs over time. The installation process is more labor-intensive and requires more time and specialized knowledge compared to SPF roofing.
Built-up roofs are durable and resistant to foot traffic, making them a good choice for roofs with heavy equipment or those that require regular access. However, they're not as energy-efficient as SPF roofs and can add significant weight to the building's structure.
3. Modified Bitumen Roofing
Modified bitumen roofing is similar to BUR but uses sheets of asphalt that have been modified with plastic or rubber additives for improved performance. These sheets are typically installed in multiple layers using heat (torched down), cold adhesive, or self-adhesive.
Modified bitumen roofing can be less expensive than SPF roofing but typically doesn't last as long and isn't as energy-efficient. The installation process can be more labor-intensive than SPF, but it does provide a robust, waterproof, and durable roofing system.
This roofing type is well suited to buildings in colder climates, as the modified bitumen is flexible even in low temperatures and resistant to the cracking that can occur with thermal expansion and contraction.
4. Metal Roofing
Metal roofing is a common choice for commercial buildings due to its durability, long lifespan, and range of style options. It's typically more expensive upfront than other roofing types but can last for decades with proper maintenance.
While installation of metal roofing can be labor-intensive, its lightweight nature often allows it to be installed over existing roof systems, saving on tear-off and disposal costs. However, metal roofs do not provide the same level of insulation as SPF roofs, often requiring additional insulation to meet energy efficiency goals.
Metal roofing is suitable for a wide range of situations, especially where long lifespan, durability, and aesthetics are key considerations. However, they may require additional insulation to meet the energy efficiency provided by SPF roofing.
In conclusion, while each roofing system has its strengths and weaknesses, spray polyurethane foam roofing offers several significant benefits, including superior energy efficiency, durability, and ease of installation, that make it an attractive option for many commercial roofing applications. As always, the specific needs and circumstances of the building should be taken into consideration when selecting a roofing system.
The Upshot
Choosing the right roofing system for a commercial building can be a challenging process, given the many considerations to weigh in, including cost, durability, energy efficiency, and installation complexities. With the wide array of roofing systems available in today's market, making an informed decision requires a comprehensive understanding of each system's pros and cons. Now that you've learned all about spray foam roofing, set up a call with our experts. In a free, 30 minute consultation, they can provide you with customized guidance.
Schedule a Free Call
Hop on a call with a GIDEON expert and learn more about how GIDEON can help you with your commercial roofing project.
Eric Schlossenberg started roofing when he was 24 years old, when he went to work as a Conklin contractor. Over the course of his career, he’s installed hundreds of thousands of square feet of roofing systems, but he still has a special passion for where he started in roof foam and coatings, and is a founding member of The Roof Coaters Guild of America. Gregarious and outgoing, Eric brings a unique sense of fun to his work, whether he’s on a roof or in the office.