The Pros & Cons of Spray Foam Roofing
April 13th, 2023 | 10 min. read
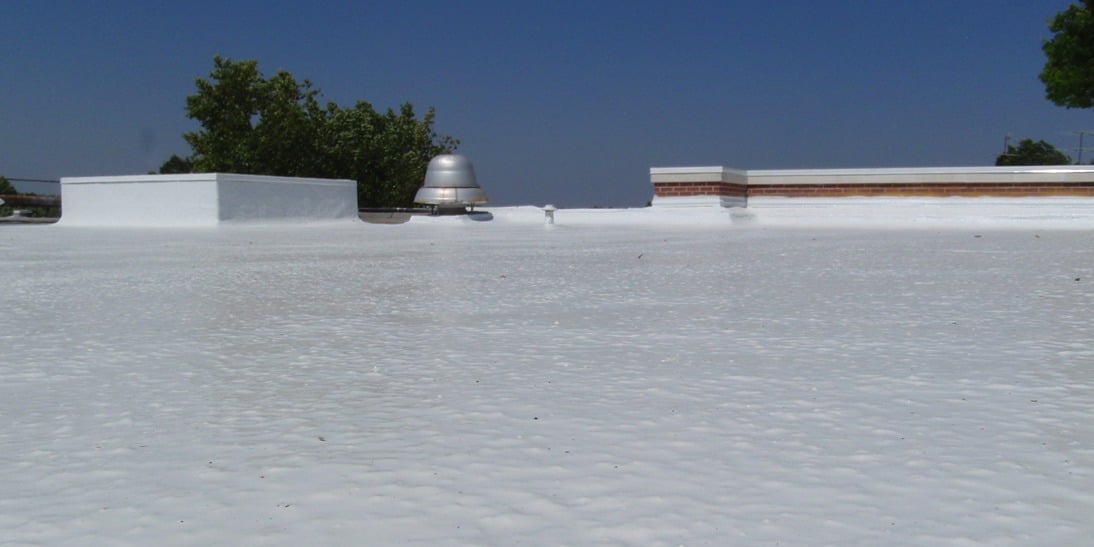
You may have heard mixed reviews of spray foam roofing. Some contractors love it. Some don’t. How do you, as a non-expert, know whom to trust? Is spray foam the roofing system of your dreams…or a nightmare?
Fortunately, at GIDEON, we’ve installed millions of square feet of every type of commercial roofing, from asphalt roofs to - yes - spray foam, and we know the ins and outs of every system.
The following article will review the pros and cons of spray foam roofing and help you determine if it’s a good solution for you.
What is Spray Foam Roofing?
Spray foam roofing, also known as “spray polyurethane foam” or SPF is a fluid-applied insulation material typically used on commercial roofs. It is a mixture of two chemicals that expand and harden to form a solid, seamless, and tough membrane when mixed and sprayed onto a surface. Introduced in the 1960s, SPF is one of the most effective insulation materials in the world and can last up to fifty years if maintained properly.
SPF is typically installed along with an elastomeric roof coating. This extremely tough, durable coating is applied over the foam and protects it from the elements, including rain, sun, and hail.
Pros of Spray Foam Roofing
It is the Most Energy Efficient Insulating System in the World
Spray foam roofing has one of the highest R-values of any insulating material, at 7 per inch of thickness. The R-value of insulation measures the “thermal resistance” of a material. Thermal resistance essentially measures how well a material insulates, i.e. prevents the flow of heat. Only polyiso foam board (which is made from the same chemical combination) insulates as well as spray foam, as you can see in our comparison chart below:
Material |
What It Is |
R-Value |
Fiberglass Batts |
Fine-glass fibers, typically used to insulate walls, floors, and ceilings in residential construction. |
2.9-3.8 per inch |
Cellulose loose-fill |
Made from recycled paper products, blown into spaces |
3.2-3.8 per inch |
Expanded Polystyrene (EPS) |
Rigid foam board made from polystyrene. |
3.6-4.2 per inch |
Extruded Polystyrene (XPS) |
Rigid foam board made from polystyrene. |
4.5-5.0 per inch |
Polyisocyanurate (polyiso) |
Rigid foam board made from isocyanate and polyol (like spray foam but a hard board) |
5.6-6.8 per inch |
Spray Foam Roofing |
Fluid-applied isocyanate and polyol |
7.0 per inch |
As you can see, spray foam outperforms every other material on thermal resistance.
Where SPF shines, however, is in the U-Value. Whereas the R-Value measures the thermal resistance of an insulating material in isolation, the U-Value measures the thermal resistance of an insulating system as a whole. What does this mean? The R-value does not consider energy flow between other materials or spaces in the system.
Air, for instance, can move through the seams between different insulation boards or other parts of the roof system. This airflow is called “thermal bridging” and is especially common in single-ply systems like TPO when they are mechanically attached. In fact, so much air can flow through a mechanically fastened TPO system that it is sometimes possible to see the membrane moving slightly in high winds.
Meanwhile, the metal plates and screws that hold insulation material like rigid foam board in place are sites of “thermal shorting,” a similar phenomenon in which the metal conducts energy between the insulation boards.
Why does spray foam have a better U-value? Because it creates a complete “thermal blanket” of insulation over every inch of the system. There are no gaps and seams to allow thermal bridging or uncovered metal plates and screws to permit thermal shorting.
Because of these superior insulating qualities, spray foam can substantially reduce HVAC load, saving you money on both energy costs and HVAC maintenance. In fact, research by Texas A&M has concluded that a spray foam roofing system can pay for itself entirely in 5 years.
It’s The Most Waterproof Insulation System
Spray foam is the most waterproof kind of insulation for six reasons:
1. It eliminates seams and joints.
Unlike rigid boards or fiberglass, SPF is a seamless, monolithic membrane that fills in or covers all existing seams and joints in the underlying roof system. Because sealant failure at the joints and seams nearly always causes leaks, spray foam has a huge waterproofing advantage.
2. SPF conforms to irregular surfaces.
Because it is fluid-applied, spray foam will conform to an irregular surface, eliminating gaps through which water can potentially flow. This also allows you to level out any depressions and eliminate ponding water, which is when water pools on a flat roof for long periods of time, eventually breaking down the material underneath.
3. Foam roofing has a closed-cell structure.
It’s composed of tiny cells that are closed and tightly packed together, making it highly resistant to water penetration. If the foam is punctured, water will not flow into the other cells. Other systems, like fiberglass, are composed of open cells, so water will flow throughout the material if the surface is punctured.
4. Spray foam expands and contracts with temperature.
Spray foam can expand and contract with temperature, helping to maintain integrity and adhesion to the substrate. Other types of insulation, like rigid foam boards (EPS, XPS, Polyiso), do not have the same degree of flexibility and can crack and delaminate as a result of roof and building movement.
5. SPF can improve water shedding.
Because you can mold the slope and height of the foam, you can also create water diversion, including crickets (triangular structures built behind a chimney or other penetration to redirect water around it), slopes, and valleys. You can even, if necessary, give a specific corner of a roof a natural pitch.
6. Spray foam self-flashes.
Because it’s fluid-applied, SPF does not need separate flashing details to seal seams between vertical and horizontal surfaces, like pipes, vents, curbs, and wall flashings. It simply covers and waterproofs the seam as it’s applied. This makes it more waterproof than using separate, traditional flashing materials.
Spray Foam Is Easy To Maintain
Because SPF is installed with an elastomeric coating, it is very easy to maintain. There are no seams and joints with flashing and fasteners that can wear out and cause leaks. The entire system is protected by a seamless elastomeric coating that can be re-applied every 15-20 years, maintaining constant protection and continuously renewing the warranty.
SPF is Lightweight
Spray foam only adds only about ½ pound to ¾ of a pound of weight per square foot, depending on the thickness of the coating. In stark contrast, a built-up gravel roof can add 8 to 12 lbs per square foot, putting much more strain on the building. Single-play systems like TPO (the most popular roof system in the US) will add 2-4 lbs per square foot.
Spray Foam Is Tougher Than You Think
People are often concerned about the toughness of spray foam. They often ask, “Can you walk on it?” The answer is yes. Its toughness is enhanced by the density of the foam, added roof granules, or gravel ballast. These things will allow an SPF system to withstand hail the size of softballs. In fact, one of the most durable roof systems ever invented was a spray foam design called the “Alpha Roof System,” which frequently lasted 50 years.
Cons of Spray Foam Roofing
Overspray
Overspray occurs when the wind blows liquid foam particles off the roof. Overspray can get on handrails, plants and shrubs, windows, cars, sidewalks, even your eyeglasses. Once it hits the surface, it cures instantly, so removing it is not easy. The sun will burn away small foam particles, so a bit of overspray is not usually a significant problem. But heavy overspray will cling stubbornly and can be expensive to remove.
To eliminate overspray, an experienced applicator will take several precautions. They may use a portable “spray tent” or a special windscreen made of a PVC frame and a fabric like burlap or polyester. The fabric is porous enough to allow wind to move through it but dense enough to trap foam particles. The contractor should also install paper shielding to catch stray particles at the roof's edge.
Cars should be removed from any surrounding parking lots. It can cost up to $400 to remove foam from a car exterior hit by overspray. While this is rare, it can happen, and an ethical contractor will cover this expense for the customer.
At GIDEON, our policy is that we won’t spray that day if it's very windy.
It Can’t Be Applied In Certain Weather Conditions
Like elastomeric roof coatings, spray foam insulation cannot be applied when the temperature drops below 55 degrees Fahrenheit. If it falls below this, the foam will not form its typical closed-cell structure, ruining critical properties like strength and waterproofing.
Moisture is also an issue. Spray foam must be applied to a completely dry surface. For this reason, contractors need to be aware of dew. As our founder Eric says, “Dew is the invisible enemy.” If spray foam is applied in the early evening, dew will get trapped underneath it, and the coating will bubble and blister when the sun rises the next day. Even if the moisture is minimal enough not to cause blistering, it can still create a bubble that will prevent the foam from bonding to the surface.
It is vital that contractors remove dew from the roof every morning and stop working before the dew falls in the evening.
It Can Be Difficult to Find a Qualified Foam Roof Installer
True expertise in foam and coatings is rare, and many customers have bad experiences with spray foam roofing and elastomeric coatings. Many crews neglect proper surface preparation before application and do not apply the foam correctly. It is vital to thoroughly vet contractors beforehand, and finding a qualified crew may be difficult.
As mentioned in the last section, inexperienced contractors frequently do not thoroughly prepare the substrate by removing debris and moisture. An old saying in the roofing world encapsulates an unfortunately common attitude: “F*** it, foam it.” Contractors with this attitude will spray over water, over plant growth like lichens and vines, etc., and cause tremendous problems down the line.
Another common problem with inexperienced contractors is applying the coating too thinly or too thickly. Why is this a problem? Well, heat is necessary for the chemical reaction that cures the foam. Too little heat will prevent the chemical reaction that creates the closed-cell structure critical to the foam’s performance qualities. Too much heat, however, can blow the cells apart after they form. If the foam is too thin, there will not be enough heat. If it’s too thick, there will be too much heat. Only an experienced, well-trained installer can do this properly.
Unfortunately, the roofing industry needs to do a better job of providing training and requiring certifications, as there are many inexperienced applicators who make numerous mistakes and eventually quit the coatings business.
Foam roofing is more complex than other types of roofing because, in a sense, you’re manufacturing the product on-site, so skill and quality control are more necessary than ever. You have to understand the material you’re working with and have the patience and attention to detail essential to craft a good product.
With What Roof Systems Is Spray Foam Compatible?
Spray foam roofing can be applied on top of most roofing materials, including:
Built-Up Asphalt Roofs. As long as the existing roof is healthy and moisture-free, SPF can be applied. As with all roofs, thorough cleaning and debris removal is crucial.
Single-Ply. Single-ply systems like TPO, PVC, and EPDM are compatible with spray foam roofing. Sometimes, a special primer is necessary to increase adhesion to the substrate. Single-ply also must be screwed down every 2ftx2ft square for the foam to not pull the membrane up off the roof. Foam is constantly under tension, so it will lift the substrate up if it’s not well-secured.
Metal Roofs. SPF can be applied to metal roofs, provided they are in good condition and free of rust, although if there is rust, it can be taken care of with a special primer. SPF can be installed on both exposed-fastener and standing-seam metal roofs. It will add 60% shear strength when applied.
Concrete Roofs. These roofs typically require an epoxy primer before foam application for proper adhesion. If the moisture content is too high, concrete may not be a good candidate for foam.
Modified roofs and tar and gravel roofs. If you coat a tar and gravel roof with an elastomeric coating, foam is an excellent choice because it will smooth the surface beautifully.
Steep-Slope Asphalt Shingles. Foam works very well for a steep-slope, shingled roof, but it’s not usually applied because it makes the structure look like a gingerbread house. So, if looks aren’t a concern (or you like the look of a gingerbread house), spray foam might be for you.
The Upshot
If you want to save money, improve the energy efficiency of your building, and install a system that won’t give you headaches down the road, then a foam roof can be an excellent choice. But foam installation can go wrong in many ways, so it is crucial that you pick the right contractor and understand how spray foam roofing works. Now that you’ve been empowered by GIDEON with a thorough understanding of foam roofing, it’s time to set up a free call with one of our roofing experts, who can assess your needs and help you craft the right solution for your roof.
Schedule a Free Call
Hop on a call with a GIDEON expert and learn more about how GIDEON can help you with your commercial roofing project.
Eric Schlossenberg started roofing when he was 24 years old, when he went to work as a Conklin contractor. Over the course of his career, he’s installed hundreds of thousands of square feet of roofing systems, but he still has a special passion for where he started in roof foam and coatings, and is a founding member of The Roof Coaters Guild of America. Gregarious and outgoing, Eric brings a unique sense of fun to his work, whether he’s on a roof or in the office.