Standing Seam Metal Roofing: A Complete Guide
August 8th, 2023 | 14 min. read
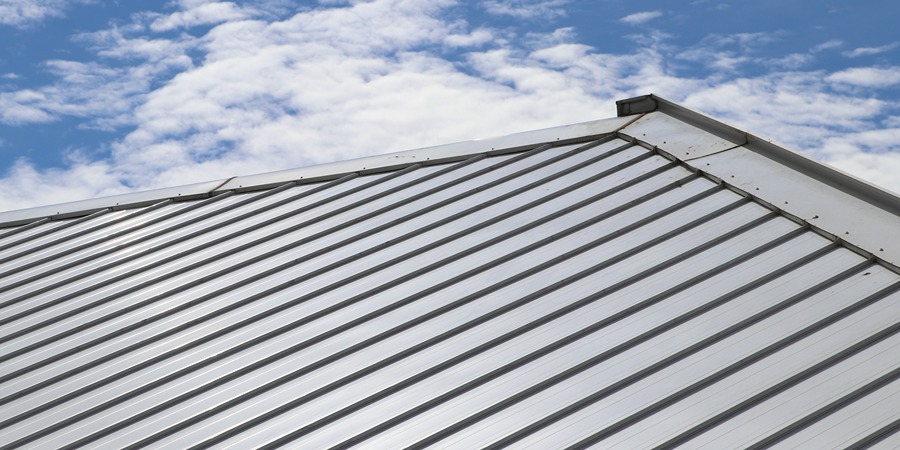
Standing seam metal roofing has become an extremely popular metal roofing option, for both residential and commercial buildings.
But how do you know if it's right for you?
If you've heard about standing seam metal roofing but are unsure about exactly what it is, what it's benefits are, or how it's installed, you've come to the right place.
Here at GIDEON, we've spent over 20 years helping both building owners and contractors navigate the complexities of commercial roofing - demystifying the process and helping you get the right solution.
In this article, you'll get an in-depth understanding of standing seam metal roofs. You'll learn everything from its working principles, advantages, and challenges to its installation process, and comparison with other roofing materials.
Strap in for a comprehensive tour of this innovative metal roof design.
Table of Contents
- What is Standing Seam Metal Roofing?
- How a Standing Seam Roof Works
- Materials Used in Standing Seam Metal Roofing
- Different Types of Standing Seam Metal Roofing
- Advantages and Disadvantages of Standing Seam Metal Roofing
- Standing Seam Metal Roofs vs Other Metal Roofs
- The Installation Process of Standing Seam Metal Roofing
What is Standing Seam Metal Roofing?
Standing seam metal roofing is named so due to its unique construction. The roofing panels run vertically from the ridge of the roof all the way down to the eaves. The edges of these panels have high seams, or 'legs', that stand up vertically, hence the term 'standing seam'. These seams are interlocked and crimped together, forming a tight seal that guards against the elements.
Now, let's delve deeper into a few specific components of standing seam metal roofing:
-
Seams: The seams in a standing seam metal roof are a significant feature. They are raised, or 'standing', which does a stellar job at preventing water penetration. Additionally, the fact that the seams are secured and raised means there are fewer seams on the roof's surface, further minimizing potential leak points.
-
Panels: The panels of a standing seam metal roof can be made from various materials, including aluminum, steel, copper, and zinc. They are typically coated for additional protection against the elements. The panels are often quite wide, ranging anywhere from 12 to 18 inches.
-
Fasteners: Standing seam metal roofs utilize concealed fasteners. The fasteners are hidden from view, offering a clean and sleek look while also providing superior weather resistance as they are not exposed to the elements.
How a Standing Seam Roof Works
Two of the biggest vulnerabilities of traditional metal roofs are exposed fasteners and expansion and contraction. Due to the expansion and contraction of the metal, exposed fasteners that penetrate the panels can wear out and even pop out, creating leaks points. The standing seam metal roof eliminates this problem by a ) hiding the fasteners beneath the standing seams, and b) fastening the panels to the deck via a clip system that gives the panels some leeway to expand and contract without damaging the roof or losing waterproofing coverage.
Hidden Fasteners
Unlike traditional corrugated metal roofs, whose panels are adhered to the deck with exposed fasteners (as seen in the picture on the left), Standing seam metal roofing systems have exposed fasteners only along the ridges and eaves (as seen in the picture on the right). They utilize concealed fasteners or clips to secure the roofing panels to the roof deck. These clips or fasteners are hidden in the seams between panels, which not only helps maintain the roof's clean aesthetics but also provides a protective barrier against weather elements, reducing the chance of fastener corrosion or failure.
The panels are joined together along their length via the standing seams. These seams, which stand up vertically from the roof surface, interlock to form a tight, weatherproof seal that hides the fasteners. This design improves the roof's resistance to wind uplift, water penetration, and even fire.
Allowing for Expansion and Contraction
Another key characteristic of standing seam roofing is its built-in allowance for thermal expansion and contraction. Metal naturally expands when it's hot and contracts when it's cold. If not properly accounted for, these changes in size can cause warping, wrinkling, or even structural failure in roofing panels.
The clips used in standing seam roofing systems are specially designed to manage this issue. They secure the roofing panels in place while still allowing them to 'float' or move laterally in response to temperature changes. The clips are fastened to the roof deck and have a top portion that attaches to the roof panels, usually in the seam.
As temperature fluctuates, the panels can expand or contract along the length of these clips, thus preventing damage due to thermal movement. The vertical seams are engineered so that they maintain their watertight connection even as the panels move, ensuring the roof remains secure and weatherproof despite daily and seasonal temperature swings.
This intricate working mechanism of standing seam roofs—hiding fasteners and permitting movement—accounts for the system's durability, longevity, and increasing popularity in both residential and commercial roofing.
Standing seam metal roofing is a brilliant blend of form and function, offering both a visually appealing look and robust protection against the elements. It's no wonder more and more building owners and property managers are considering standing seam metal roofs for their properties.
Materials Used in Standing Seam Metal Roofing
Galvanized Steel
One of the most common materials used in standing seam metal roofing is galvanized steel. This type of steel is coated with a layer of zinc, which helps protect it against corrosion and rust. Galvanized steel is a cost-effective option that provides excellent durability and longevity.
Galvalume Steel
Another steel variant used is Galvalume steel. This is a step up from galvanized steel as it is coated with a mix of aluminum, zinc, and silicone. This combination offers a better defense against corrosion - outperforming galvanized steel in most situations. However, it can be pricier.
Aluminum
Aluminum is another material commonly used for standing seam roofs. It's lightweight, corrosion-resistant, and highly durable. Aluminum is an excellent option for coastal areas as it withstands salt spray better than steel.
Copper and Zinc
For a more premium option, you might consider copper or zinc standing seam roofs. These materials are naturally corrosion-resistant and offer a unique, eye-catching appearance. While they are more expensive than steel or aluminum, they can last for many decades with proper maintenance.
Remember, the choice of material is crucial as it affects the roof's durability, maintenance requirements, cost, and appearance. Consider your specific needs, budget, and local climate when making your choice.
Each material has its own pros and cons. So, what's the best choice for you? It depends on your specific requirements and preferences. The key is to strike the right balance between cost, durability, and aesthetic appeal.
Different Types of Standing Seam Metal Roofing
Snap Lock
In a Snap Lock system, the standing seams have a special design that allows them to snap together when overlapped. They don't require hand or mechanical seaming. However, this system thrives best when there's an underlying layer of decking, such as plywood. If we're dealing with a commercial building without decking, where the panels are simply laid on the purlins, it's a different story. In this scenario, if wind enters the building, it can break the snap-lock and wreak havoc on your roofing system. For buildings of this nature, a mechanical lock system becomes necessary.
Mechanical Lock
In a mechanical lock, each standing seam panel edge has a vertical leg: one male leg, which goes on the inside, and a female leg, which goes on the outside. The male leg is installed downwards, after which the fastening clip is secured over it. Then, the female leg of the panel goes over the clip and male leg. These parts are then tightly seamed together using a hand-held tool or a mechanical seamer.
Mechanical locks can be crimped and folded at 90 degrees (a Single Lock) or 180 degrees (a double lock).
There are typically two types of mechanical locks you'll find in this roofing system: the 1" and 1.5" mechanical lock profiles. What's the difference?
-
1" Mechanical Lock: This is the most common profile used for residential projects. It's suitable for roof slopes 3:12 and greater, meaning it can be used on fairly steep roofs. It's also ideal for smaller roofing projects due to its manageable size.
-
1.5" Mechanical Lock: This profile is used in commercial and larger residential projects. It's designed for low to steep sloped roofs, making it versatile for different building designs. The larger size provides a more robust lock, which is beneficial for larger roof areas.
Choosing the right mechanical lock for your standing seam metal roof depends on the specifics of your project, including roof size, slope, and architectural design. But remember, the importance of a good mechanical lock cannot be overstated. It's the linchpin that holds your roof together, ensuring durability and longevity.
So, the next time you're considering a standing seam metal roof, don't overlook the importance of the mechanical lock. It's not just a minor detail, but a vital component that contributes significantly to the overall performance and lifespan of your roof.
Whether you're installing a new roof or replacing an old one, understanding the workings of the mechanical lock can make all the difference. Knowledge, as they say, is power—and in this case, that power translates to a more secure, durable, and long-lasting roof for your building.
Nail Strip
In a nail flange profile, also known as a nail strip or fastener flange, fasteners connect the male leg directly to the deck. After fastening the male leg, the female leg of the panel neatly snaps over it to cover the fastener.
This method removes the clip system, so it's not as durable or weather-resistant as Snap Lock or Mechanical Lock designs.
In conclusion, understanding the different types of standing seam metal roofing is crucial in determining the best option for your property. Whether it's the easy-to-install Snap Lock, the weather-resistant Mechanical Lock, the efficient Nail Strip, or the aesthetically pleasing Batten Seam, rest assured there's a type perfectly suited for your building's needs.
Advantages and Disadvantages of Standing Seam Metal Roofing
Advantages of Standing Seam Metal Roofing
-
Leak-resistance: Standing seam designs dramatically reduce the likelihood of leaks compared to traditional exposed-fastener panels because there are no screws penetrating the vertical seams, and because standing seam roofs can accommodate longer panels, which translates to fewer seams.
-
Easily withstands expansion and contraction: Standing seam's floating clip design is an excellent solution the a traditional metal roof's vulnerability to expansion and contraction.
-
Longevity: With proper installation and maintenance, standing seam metal roofs can last up to 50 years or more.
-
Weather Resistance: Standing seam metal roofs are highly resistant to extreme weather conditions, including heavy rain, hail, snow, and wind. This makes them an ideal choice for all sorts of climates.
-
Fire Resistance: Metal roofs are non-combustible, providing an added layer of protection against fire.
-
Environmentally Friendly: Metal roofing materials are often made from recycled materials and can be recycled at the end of their life cycle.
Disadvantages of Standing Seam Metal Roofing
While standing seam metal roofing is widely acclaimed for its myriad of advantages, like anything else in life, it's not without its downsides. Let's take a balanced look at a few potential drawbacks that might make you pause for a moment before jumping on the metal roofing bandwagon.
-
Cost: One of the most significant drawbacks of standing seam metal roofing is the initial installation cost. This type of roofing tends to be more expensive than traditional metal roofing as well as common single-ply systems like TPO, so it could take a larger chunk out of your budget.
-
Installation Difficulty: The installation of standing seam metal roofing requires a certain level of expertise and experience. It's not a task for a novice do-it-yourselfer, and even many professional roofers may not be properly qualified. Finding a great installer can be harder that it is for more common roof types, like TPO or exposed fastener metal.
-
Noise: During a heavy rain or hailstorm, a metal roof could be noisier than other roofing materials, although proper insulation can help mitigate this concern.
-
Color Match: If you need to replace a panel or two in the future, matching the color could be a challenge. The new panels might stand out against the weathered existing ones.
Standing Seam Metal Roofs vs Other Metal Roofs
Metal roofing, particularly standing seam metal roofs, are unique. They differ from other metal roofs in structure, benefits, applications, and costs. Let's explore these aspects.
Standing Seam vs Corrugated Metal Roofs
Often seen on barns or warehouses, corrugated metal roofs are a common sight in both urban and rural settings. They feature a distinctive "wavy S" pattern of ridges and grooves, a design that enhances the panel's strength. They're typically made from galvanized steel, galvalume, or aluminum.
-
Durability: Unlike standing seam roofs, corrugated metal roofs have exposed fasteners and no "floating clip" system to allow for expansion and contraction. This makes them more vulnerable to damage and leaking over time.
-
Installation: Corrugated roofs are quite a bit simpler to install, which means they can often be a DIY project.
-
Cost: Corrugated metal roofing is quite a bit cheaper due to its simpler design.
Standing Seam vs R-Panel Metal Roofs
R-panels are a more modern exposed-fastener design, with straight ribs and sharp angles rather than rounded ones. They're the most common type of exposed fastener panel in use today.
-
Durability: R-Panel roofs, like corrugated metal roofs, also have exposed fasteners, meaning they suffer from similar vulnerabilities with regards to leaks and expansion and contraction.
-
Installation: Because they use exposed fasteners, the installation process of R-panel roofing is generally considered less complex compared to that of standing seam roofs.
-
Cost: R-panel roofs are less expensive upfront, but they require more maintenance over time, which could lead to higher overall costs.
Standing Seam vs Metal Shingle Roofs
Metal shingle roofs, also know as "stone-coated steel" or "stone coated metal", are metal panels designed to look like traditional shingle or tile roofs.
-
Appearance: Metal shingle roofs can mimic the look of other materials such as wood or slate, while standing seam roofs have a minimalist, modern aesthetic.
-
Installation: Standing seam roofs can be more complex to install due to the need for specialized tools and precise measurements, but they often provide better weather-tightness.
-
Durability: Both types offer good durability, but the design of standing seam roofs can provide superior resistance to leaks.
-
Cost: Metal shingle roofs are usually more expensive than standing seam roofs.
The Installation Process of Standing Seam Metal Roofing
Have you ever wondered what goes into the installation process of a standing seam metal roof? As a property owner or manager, understanding the basics of this procedure can help you make informed decisions and monitor the progress once you decide to install this type of roofing. Let's break down the main steps.
A professional installer approaches the task of installing a standing seam metal roof with meticulous attention to detail, in a series of well-defined steps that ensure optimal performance and longevity of the roofing system.
1. Initial Inspection and Measurement
The standing seam metal roof installation begins with a thorough inspection of the existing roof. This involves assessing any signs of damage, irregularities, and taking precise measurements of the roof's length, width, and slope to estimate the necessary amount of materials.
2. Roof Deck Preparation
Following the initial assessment, the installer moves on to preparing the roof deck. This stage involves stripping away any old roofing material, ensuring the surface is clean, flat, and free from protruding elements.
3. Underlayment Application
The next phase is to secure the underlayment across the cleaned roof deck. Typically made of synthetic or rubberized asphalt, this underlayment is fastened securely, providing a protective layer against water and wind-driven rain.
4. Standing Seam Panel Preparation
Once the roof deck is ready, the standing seam panels are cut to the appropriate length based on the earlier roof measurements. These calculations account for necessary overhangs to ensure a professional finish.
5. Panel Installation
The installer begins setting up the panels from one end of the roof, usually opposite to the prevailing winds. Each panel is aligned with precision, ensuring it's square with the eave and the ridge to set the standard for the rest of the installation.
6. Application of Clips
As the panels are being installed, the installer systematically applies clips at specified intervals along the seam. These clips are crucial in securing the panels to the roof deck and allowing for roof contraction and expansion due to temperature variations.
7. Interlocking and Seaming
With each new panel, the installer ensures it interlocks with the vertical seams of the previous one. A seam closing tool is then used to mechanically crimp and seal the panels together, thus forming a watertight seal.
8. Flashings Installation
After all panels are installed, the focus moves to flashings. These are strategically placed at various points on the roof like edges, corners, ridges, valleys, and around roof penetrations. Flashings serve to direct water off the roof and prevent infiltration.
9. Final Inspection
Once the panel and flashing installations are complete, the installer conducts a final inspection to ensure the integrity of the installation, with secure panels, properly sealed seams, and correctly positioned flashings.
10. Cleanup
The installation process concludes with a thorough site cleanup, removing any leftover metal scraps or sharp objects that could pose potential hazards.
This step-by-step process, when carried out by a professional, guarantees the optimal performance of the standing seam metal roof, providing durability and weather protection for years to come.
The Upshot
Choosing a roof for your building is no small task, given the myriad of options available. And the complexity only increases when you're trying to balance durability, aesthetics, pricing, and being good to the environment. This is especially true for standing seam metal roofing, which, requires detailed expertise for successful installation.
Now that you've learned the essentials of standing seam systems, reach out to us at GIDEON for personalized guidance. Whether you're contemplating a new roofing project or considering an upgrade, we're here to help. Contact us today to schedule a free 30 minute consultation or to learn more about how we can help make your standing seam metal roofing project a resounding success.
Schedule a Free Call
Hop on a call with a GIDEON expert and learn more about how GIDEON can help you with your commercial roofing project.
Eric Schlossenberg started roofing when he was 24 years old, when he went to work as a Conklin contractor. Over the course of his career, he’s installed hundreds of thousands of square feet of roofing systems, but he still has a special passion for where he started in roof foam and coatings, and is a founding member of The Roof Coaters Guild of America. Gregarious and outgoing, Eric brings a unique sense of fun to his work, whether he’s on a roof or in the office.