The Basic Components of a Commercial Roof System
June 16th, 2023 | 7 min. read
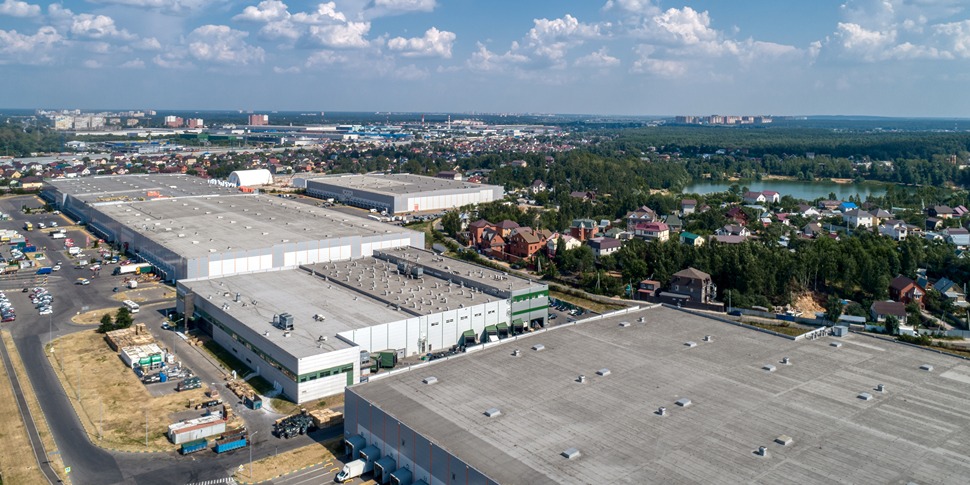
Replacing or repairing a commercial roof can be a 5 - or even 7 - figure decision that can dramatically impact your business. Unfortunately, many building owners and property managers have only a cursory understanding of what goes into their roof, making it difficult to properly evaluate roofing contractors and quotes.
While there are numerous factors to consider when purchasing a roof repair or replacement, one of the best places to start is to simply familiarize yourself with the roof’s fundamental components. At GIDEON, we've spent two decades helping clients clearly understand what goes into their roofs, and in this article we break it all down. By the end, you’ll have a clear picture of a commercial roof’s basic structure.
Table of Contents
The Membrane
The roof membrane is the outermost layer of the roof system, the first line of defense against rain, snow, wind, hail, and damaging UV rays. Because it takes a beating from the elements, it needs to be versatile enough to handle any kind of weather condition.
There are several types of membrane commonly used on flat roofs, each with unique chemical properties that make them suitable for different applications. These include:
Single-Ply Membranes: These consist of a single layer (or “ply”) of material that comes in sheets of a particular size which are laid over the insulation and fixed to the decking as a complete assembly. The 3 common types are TPO, PVC, and EPDM (Rubber). These are the most commonly used membranes, with TPO alone making up 40% of commercial flat roofs.
Metal Roofs: Made from materials like steel and aluminum, metal membranes (or panels) are tough and very long-lasting. There are two primary types: exposed fastener and standing seam.
Built-Up Roofs (BUR): This type of roof is made from alternating layers of bitumen (asphalt) and reinforcing fabrics. BUR systems were the go-to roofing choice for over a century before being overtaken by TPO single-ply membranes.
Fluid-Applied Membranes: These membranes are sprayed or rolled onto existing roofs where they cure into a tough, durable covering that protects and restores an aging roof. They consist of elastomeric coatings and are becoming more popular as they can substantially improve the strength, longevity, and energy-efficiency of an existing roof, at a comparatively low price. They are also an increasingly popular choice for helping organizations achieve sustainability objectives, as they produce very little waste and reduce overall energy consumption.
Modified Bitumen: These membranes consist of asphalt (bitumen) modified with plastic or rubber polymers to enhance their performance characteristics. The two common types are Atactic Polypropylene (APP) and Styrene-Butadiene-Styrene (SBS).
The Coverboard
A cover board is a board that goes between the membrane and the insulation. While not an essential part of a flat roof system, cover boards are often added to increase the strength and durability of single-ply membranes, making them more resistant to hail strikes and providing a harder surface for foot traffic.
The Insulation
The next major component of a flat roof system is the insulation, which serves to block the loss or the intrusion of thermal energy, depending on the time of year. Insulation is a particularly important element of the roof system for two reasons. Firstly, it is the single largest contributor to variations in cost - changing the insulation type can increase or reduce your bid price dramatically. Secondly, it is the only component that can turn your roof into a positive investment, i.e., it can turn the roof from a net cost to a net savings, due to its potential to substantially reduce both your building’s energy consumption and the price that you are charged for electricity or natural gas.
There are two main categories of insulation for commercial roofs: rigid foam board and spray polyurethane foam (SPF).
The Deck
The deck is the base structure upon which all the other components are built. It provides basic structural support for the entire roof assembly.
There are a variety of materials that can be used to construct a roof deck, each with their own advantages:
Steel: Highly durable and resistant to fire, steel decks are often found in commercial buildings. They're designed to support heavy loads, and are usually coated or galvanized to prevent rust.
Concrete: Known for its strength and fire resistance, concrete is a popular choice for larger commercial or industrial buildings. While providing a robust deck, it can be very heavy and might require additional support.
Wood: More common in smaller commercial buildings, wood decks are lightweight and easy to work with. They're typically crafted from plywood or oriented strand board (OSB), and must be properly treated to resist moisture and pests.
Tectum: Made from a composite of wood fiber and cement, tectum decks are known for their capacity both to absorb sound and insulate buildings. These capabilities are a result of the porousness of the wood fiber and make tectum a popular choice for auditoriums, churches, and school gyms.
Drainage
Slope
Despite the name, flat roofs are not (or, at least, they shouldn’t be) perfectly flat. They should have a low-slope to allow water drainage. But not all low-slope roofs have a slope built into the decking itself. Most older buildings were built with flat decks, so the slope has to be constructed on top of the deck, either by pouring and molding lightweight concrete or gypsum or by constructing a tapered insulation system (a method in which the insulating foam boards themselves are tapered to create a slope).
Drains & Scuppers
Drains and scuppers are the exit points for water as it’s shed from the roof, preventing it from accumulating and damaging the roof.
Drains: Installed at the lowest points of a roof's surface, drains capture water and funnel it away through internal piping. They often include a strainer to prevent debris from entering and clogging the drainage system.
Scuppers: Scuppers are outlets installed in the parapet or sidewalls of a roof that allow water to exit the roof and fall directly off the side of the building or into a downspout. They are typically used in combination with roof drains or can be used independently on sloped roofs where water naturally flows towards the roof edges.
Overflow Drains & Scuppers: Overflow drains and scuppers provide redundant water drainage capacity. If heavy rainfall or snowmelt exceed the drainage system’s capacity, water will begin to pool on the roof for long periods, damaging the roof or even (in extreme cases) causing it to collapse altogether. Overflow drains and scuppers have lips that are usually raised 4 inches above the roof surface to remove excess water.
Penetrations
Penetrations are structures, such as pipes, vents, and HVAC units, that stick up through the roof membrane. The seams created when the membrane abuts these penetration must be carefully sealed with flashing to prevent leaks.
Common penetrations include plumbing vents, exhaust vents, HVAC Units, skylights, and roof hatches.
Flashing & Edge Details
Flashing and edge details seal off and protect the roof's vulnerable areas, such as perimeters, corners, and penetrations - essentially anywhere the roof membrane meets vertical walls, roof curbs, and other roof inventory.
Flashing
Flashings help direct the flow of water around openings or changes in the roof assembly. On a commercial flat roof, the membrane itself is used as flashing, with contractors running it up or down the adjacent surface and sealing the seams.
Penetration Flashings: These are used around roof penetrations such as vents, pipes, skylights, and HVAC units. They help to create a watertight seal and direct water away from these penetrations.
Expansion Joint Flashings: These are designed to accommodate movement between different parts of a building, preventing cracks and damage to the roofing system.
Edge Details
Edge details provide a transition between the roof and the other parts of the building. They offer protection against water ingress and wind uplift.
Gravel Stops and Drip Edges: These components are installed along the perimeter of the roof. They prevent water from seeping under the roofing material and direct runoff away from the building's façade.
Coping Caps: Installed atop parapet walls, coping caps protect the upper edges of these walls and prevent water from seeping underneath the wall flashing.
Gutters and Downspouts: Although not strictly edge details, gutters and downspouts are typically installed along the roof's edge to collect and direct runoff away from the building.
The Upshot
Making the right decision for a complex purchase like a commercial roof is no easy task, particularly when roofing contractors vary dramatically in quality and integrity. Now that you’ve learned the basic structure of a commercial roof from GIDEON, check out our guide to the most popular commercial roof system on the market, TPO. In this comprehensive guide, you’ll learn the essentials of this system, which comprises 40% of all commercial roofs in the US.
Schedule a Free Call
Hop on a call with a GIDEON expert and learn more about how GIDEON can help you with your commercial roofing project.
Eric Schlossenberg started roofing when he was 24 years old, when he went to work as a Conklin contractor. Over the course of his career, he’s installed hundreds of thousands of square feet of roofing systems, but he still has a special passion for where he started in roof foam and coatings, and is a founding member of The Roof Coaters Guild of America. Gregarious and outgoing, Eric brings a unique sense of fun to his work, whether he’s on a roof or in the office.